Am I Still Sleeping?
Openning Monologue
It's Monday, and I'm pretty sure I'm still asleep so I'll keep this week's update brief.
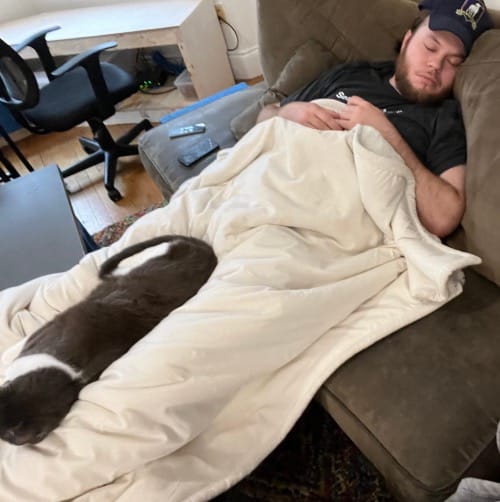
This week, DB-X production continues and hopefully final assembly comes by next Friday. I'm trying to hit a June 1st delivery date, but the end of May is packed to the brim with all sorts of extracurriculars. Everything is on track, dare I even say ahead of schedule, for now...
This Week
DB-X Ballast Machining
I'm so freakin' hyped about these!
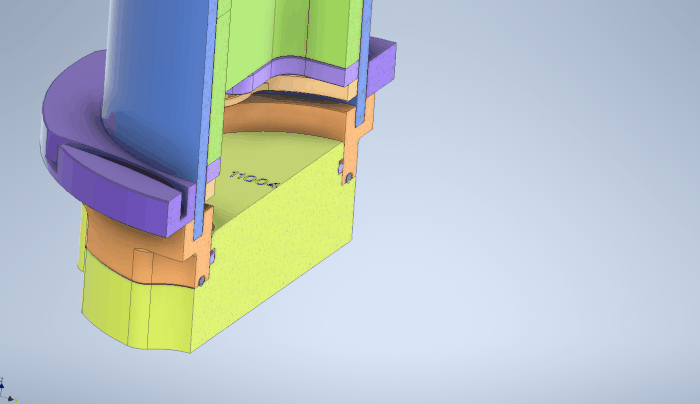
When you prototype something, you might make one or two copies of that part When you do this, you can afford to do it inefficiently. Maybe you aren't being efficient with materials. Perhaps it means there aren't any automation steps, or the flow between steps is arduous. The cost of optimizing a process doesn't amortize across a part or two, but it does start to payoff when you make 10, or 20 of something. The REV 003 ballast weight is the first machined part where I needed to make a bunch, in this case 10, and so this is the first stab at what I'll call "prototyping production".
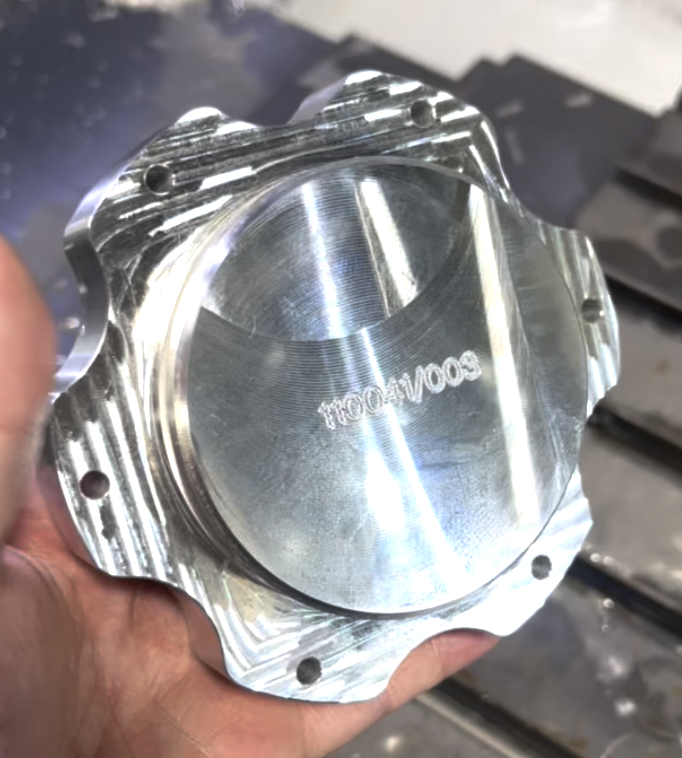
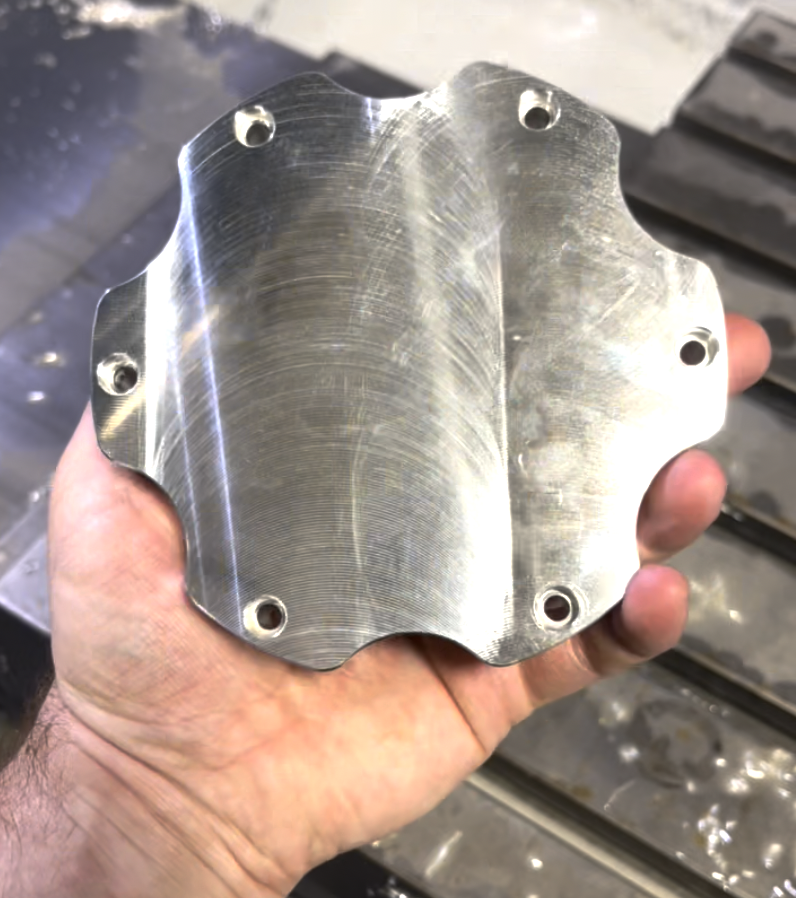
Machined DB-X Ballasts
The DB-X Ballast gets machined in two steps, you can think of it as a top side (OP1) and a bottom side (OP2). If you make one part, you'd setup and run OP1, breakdown that setup, and get OP2 setup then run that. With 10 parts, I was able to setup both OP1 and OP2 so they could run on the machine at the same time. This way I'd have two parts in the machine at once, one part ready to get OP1 machined, and another ready for OP2. When the machine finishes, I can pull out the completely machined OP2 part out; move the part from OP1 into the OP2 spot, then put a new blank piece of stock in the OP1 spot.
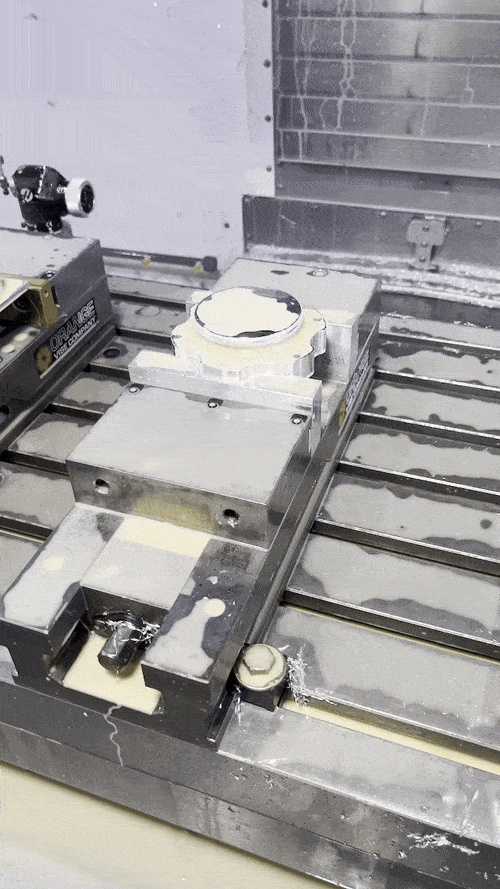
OP1 in progress part on the left. OP2 completed part on the right.
Long story short, this ends up saving a lot of time, but also increases the amount of time I can walk away from the machine for. OP1 and OP2 are both about seven minutes. If I only ran one at a time, I might get five minutes of down time between switching parts; but if I run both at the same time, I get 10-15 minutes of down time. While it's still not great for focus, I can certainly manage to turn that from idle time into productive time.
DB-X Sleeves
Each DB-X takes 6 3D printed sleeves that are captured into the PVC body tube, and provide mounting points for the electronics and batteries.
6 parts isn't so bad, but managing to print 60 parts is a bit more cumbersome. After a couple of false starts printing on Ultimaker S5 printers, I switched to the much larger format Terabot printer we have here at the shop.
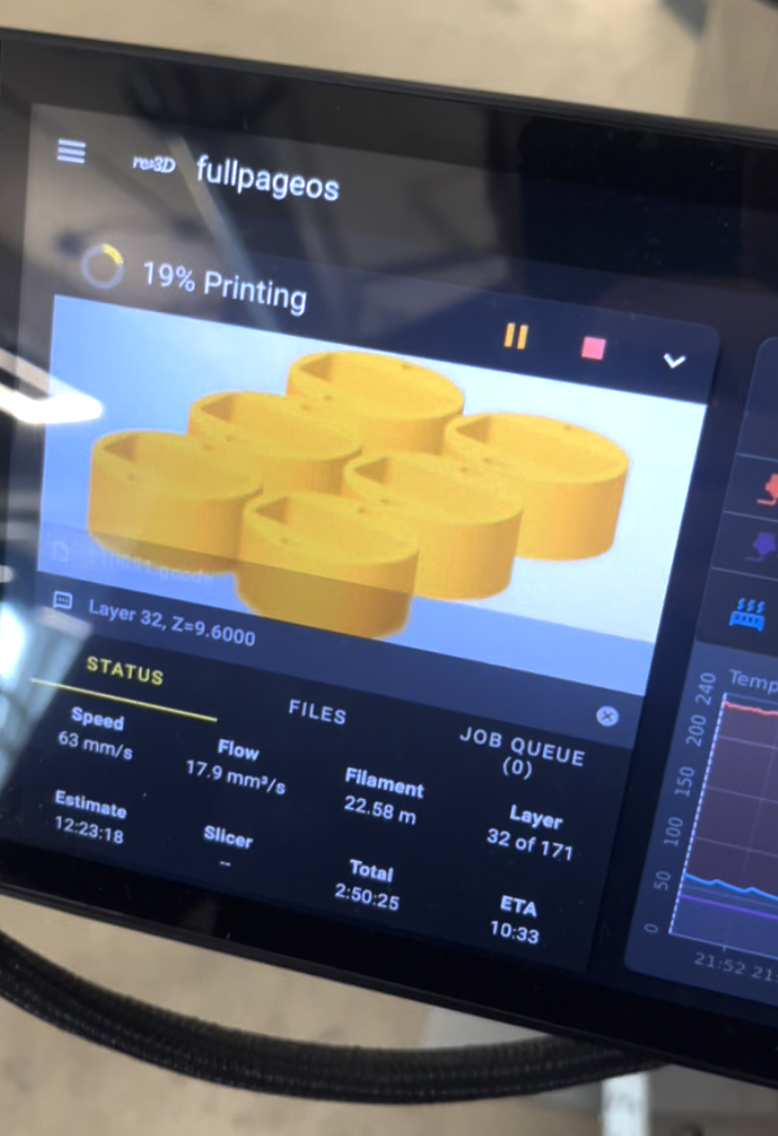
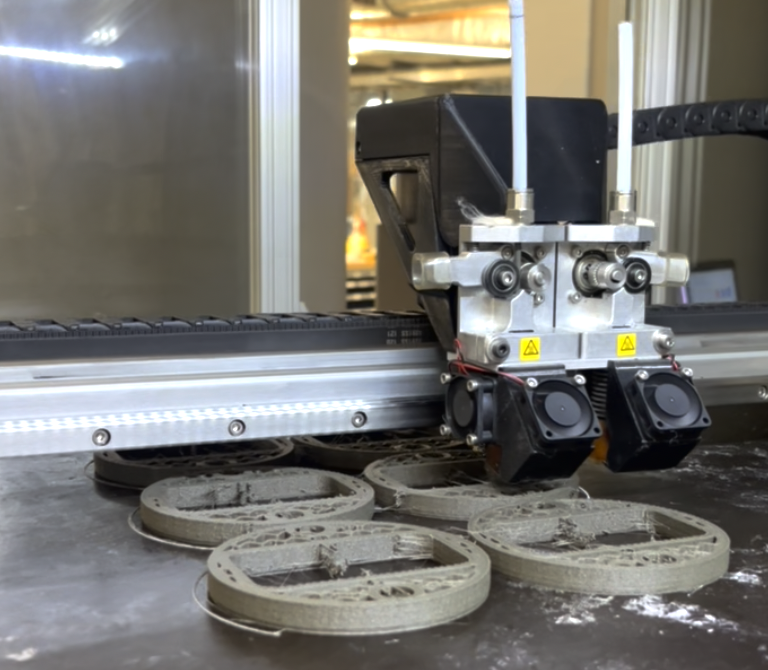
3D printing DB-X Sleeves
The Ultimakers are usually great, but were causing a lot of filament issues resulting in failed prints. I had 3 separate batches of parts all fail at abut 75-80% completion, all for different reasons... That's a huge schedule setback and a huge material waste, nearly 2kg I'd bet...
On top of that, they're usually in high demand and I didn't want to hog them for weeks at a time. They also don't have filament runout sensors - they have no idea if they've run out of ink or not, the just print until they think they're done. The Terabot on the other hand is not particularly sought after, and does have a filament runout sensor. That means it would pause my print if there were any filament problems, I could address the issue, and resume the print where it left off. This saved me a handful of times over the week, and I'm stoked to use it more in the future.
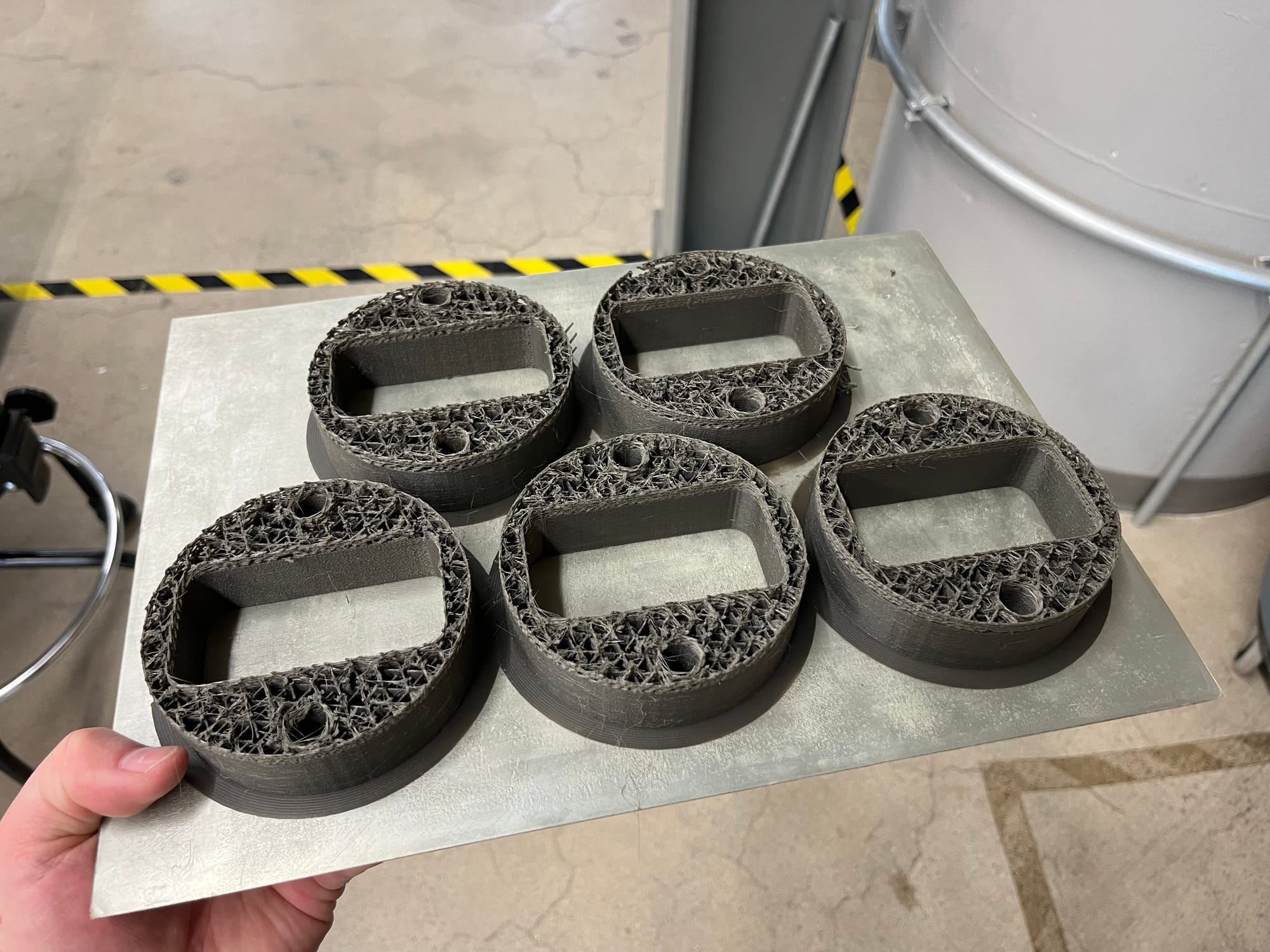
DB-X Software
After putting this off for a while, it finally got a good chunk of my attention towards the end of the week.
When NASA builds a Mars rover, they machine the parts, assemble everything together, test it and blast it off into outer space. What you might not know is that a bulk of the work isn't done yet. They're on a crazy time crunch to launch, but then they sit back and wait about 9 months for it to get there. There isn't really anything mechanical engineers, welders and technicians can do in that time, but the software engineers are still busy writing code! It's not until it gets closer to Mars, or even after its touched down on the planet's surface, does it get the full software update it needs to carry out its mission.
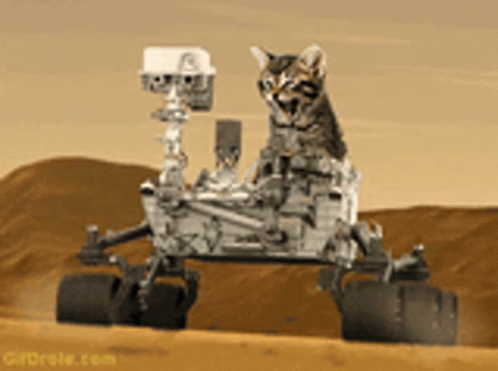
Tl;dr: You can't easily change hardware after you've shipped it, but you can very easily update and change software at any point down the road (if you plan for it).
I've largely opted for NASA's strategy here, finish the hardware first, get it out the door, then focus on software second. It can always come after delivery if necessary.
Thankfully, I've found down time to take a crack at the software before hand and while there've been many ups and downs, things are looking good. Much like the hardware side of things from last week, I'm actively fighting myself from making things more complicated than they need to be. So far I'm doing alright.
Next Week
DB-X Powder Coating
The DB-X has 2 aluminum parts on it, an electronics bracket and the ballast weight you should be familiar with by now. While I could leave them as machined, it wouldn't look as clean or finished in my opinion. To tidy things up and put my best foot forward, we're going to powder coat them both.
I've opted to sandblast the electronics bracket to knock away any burrs, scratches and imperfections; and get a nice even finish across the whole part before getting powder coated.
The ballast weight is a focal point on the buoy. Because it's exposed to the water during operations, I've opted to leave the part as machined before powder coating. A sandblasted finish could promote rapid biofouling and growth, which we don't want...
For anyone who isn't familiar with powder coat, it's a pretty slick painting process. Instead of a wet paint you roll, brush or spray on, you spray a dry powder onto the part, then bake the powder so it becomes fluid then cures. What's fun is the part and the powder are oppositely charged (positive attracts negative), so when you spray the powder, it's attracted and clings to your part!
DB-X Software Continue
Nothing really thrilling to say here. The software on the buoy is incredibly simple, the harder part is getting it linked into all the infrastructure that handles the data after it's been collected.
DB-X End Caps
These are the PVC end caps that get glued to the end of the PVC tube. They capture/secure the internal sleeves, and they provide the interfaces for mounting the ballast and top cap.
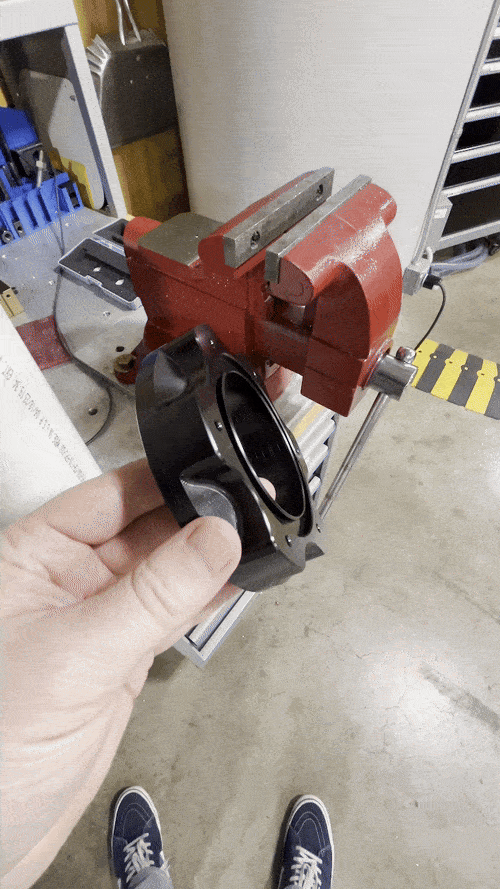
I get to flex the "prototyping production" muscles again here. I have 20 of these to make. Material arrives Monday, I should be able to machine Tuesday.
XB-X Assembly
Mostly just waiting on printed parts for this. The 3D print schedule got bumped a bit as discussed earlier. Only reason this doesn't happen is if DB-X End assembly ends up being more cumbersome than expected...
Wins
Terabot
The Terabot is slick and cruising through the 3D print workload. I thought for some reason it'd be more fickle, but maybe it's not big printers that cause problems, just big parts?
Graduation SZN
Congrats to all graduates! My girlfriend graduated from her masters program this past weekend. My brother will have his undergraduate commencement next weekend. Lots for them to proud of, and I will celebrate alongside them with complimentary Bloody Mary's (🌶️ spicy, of course 🌶️) that tend to accompany these types of occasions.
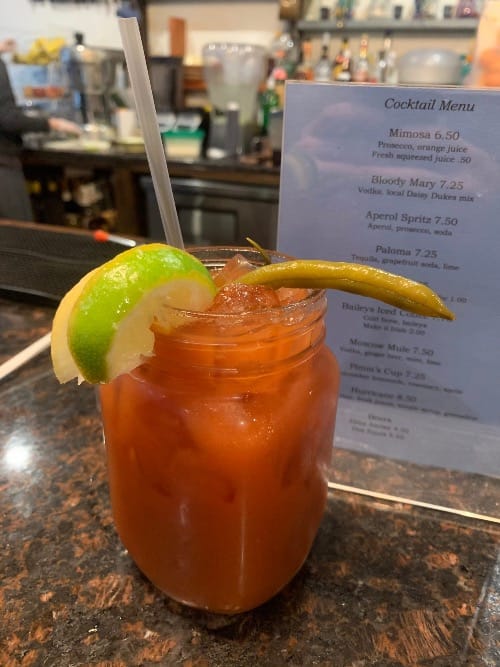
Losses
Bruins
Lots of good hockey being played right now, just not by the Bruins...
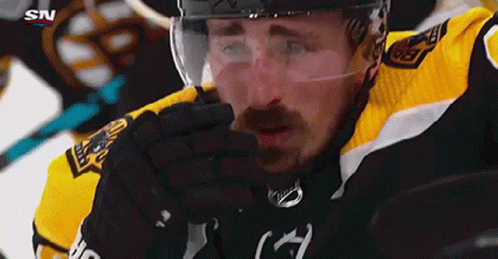
Frosted Mugs
Everyone knows Fiddlehead is served is a frosted mug. There's a new bartender at the place around the corner and he absolutely refuses to serve Fiddlehead in the chilled glass. It absolutely kills the vibe. Get it together, Jeremy, or whatever your real name is...
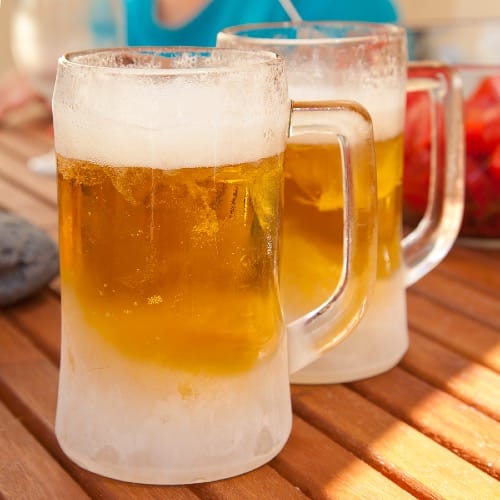
Closing Monologue
I'll tell you h'wat, I'm ready to get on the water and get these buoys deployed. We've got a long week to get there, but it's doable...
Whatever you're working on this week, good luck, and finish strong. If we work hard this week, we can play hard this long weekend.
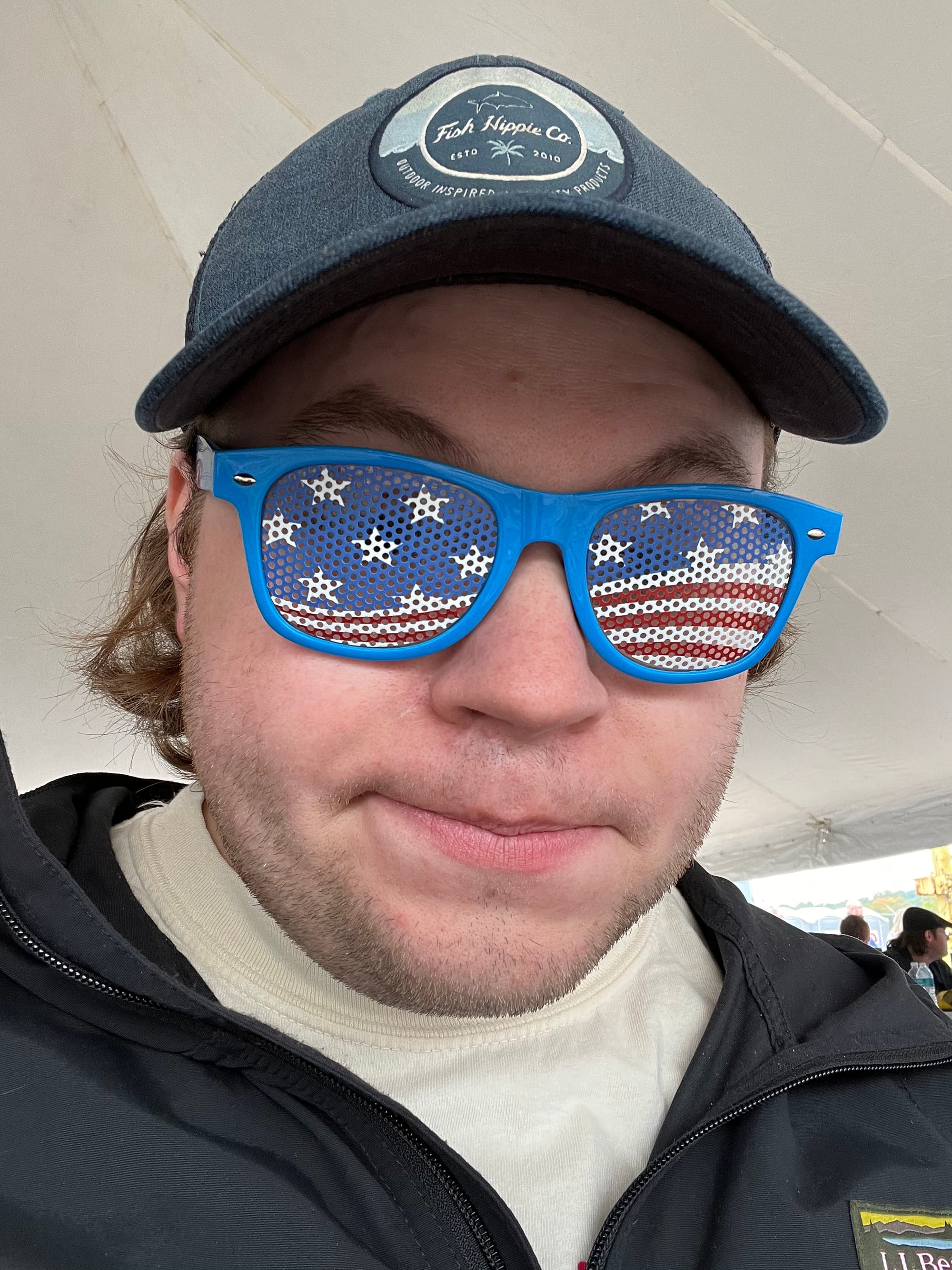