We. Are. So. Back.
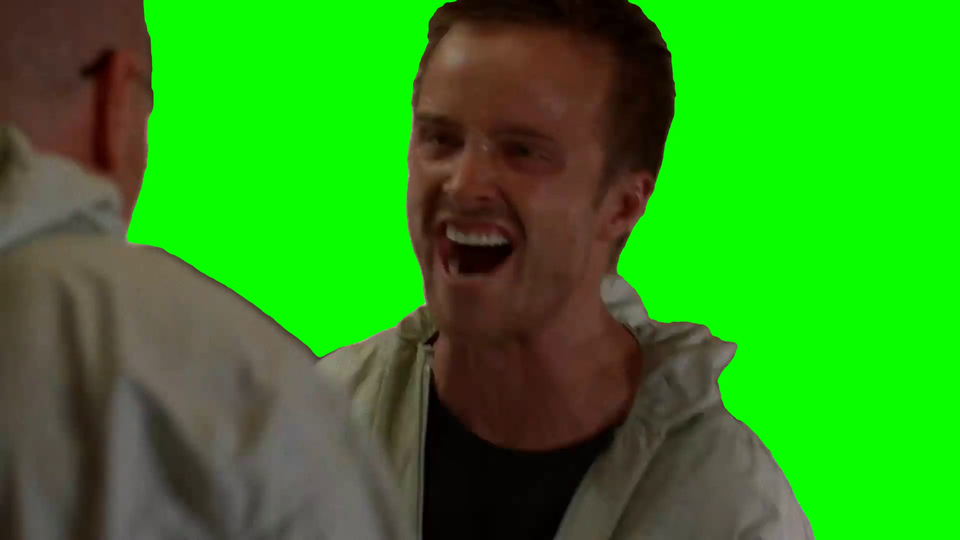
Openning Monologue
Yeah, yeah, yeah, I know...
Andy, WTF happened to the last 2 blogs?!"
I unapologetically, did not do them. The last three weeks have been flat out, full bore, all gas, no brakes.
May 19-25th
All About XB-X
I had set a deployment date with Max at Ferda Farms for Saturday the 25th. I had put the XB-X on the back burner after receiving the order for DB-X buoys, but it was time to give it some much needed attention.
I've spent 90% of the engineering effort to date, reworking the electronics enclosure and making sure that it's impenetrable. This left a lot of work on the lower half of the buoy. I started the week drilling holes in the hull for the eyebolts and sensor ports. After that, I got to designing a system to contain the ballast.
I'm not sure if I've written about the solution before, but I'll quickly recap the ballast. You need to weight the buoy down so that it sits at the right height in the water, and so that it is stable (waves knock it around, it needs to return to the right orientation). A huge block of some metal, be it aluminum, steel or vibranium, is expensive and has to be machined to match the shape of the hull. Instead, I bought a box of steel beads/powder I can just pour it into the hull until I get the weight I need for proper ballasting. Usually it's sold for bead blasting/sandblasting. It's actually a lot like sand, but way denser which is good because it takes up less volume in the hull.
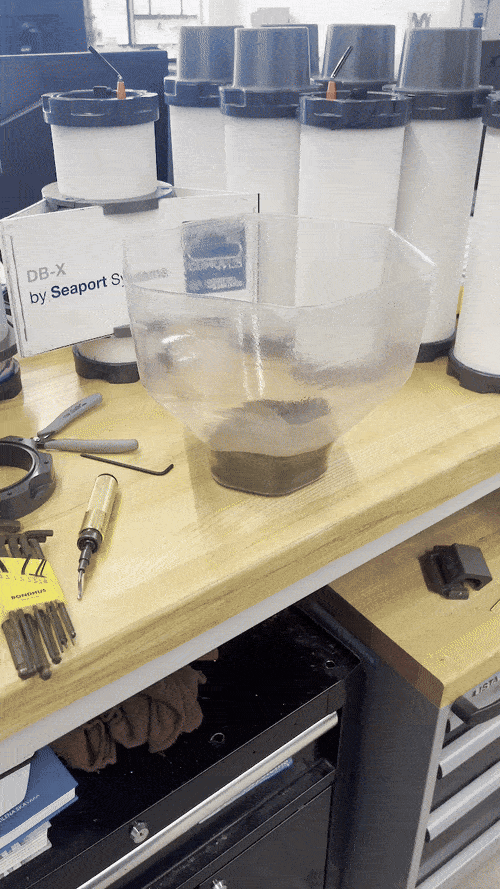
I machined a custom standoff that sits in the bottom inside of the hull and it serves two purposes. 1, it gives the eyebolt that attaches the buoy to a mooring, a sturdy place to screw into. 2, it's a spot where I can bolt a plate inside the hull that keeps the steel from sloshing around.
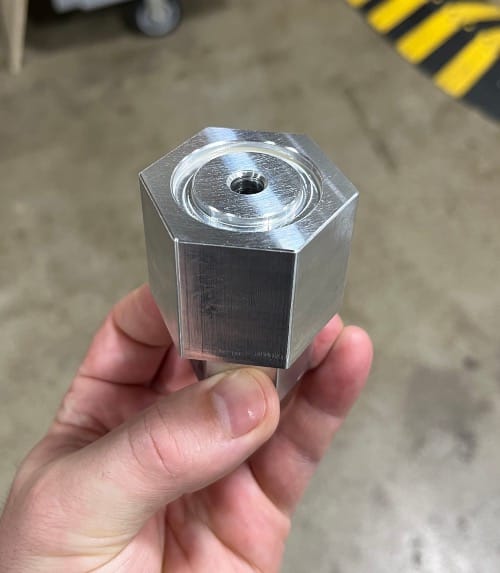
All in all I'm pretty stoked with this solution - it's easy and cheap to make, it's easy to modify later, and it makes the buoy really easy to work on!
Saturday morning I woke up insanely early to finish some final integration work before driving North to Ferda Farms where I deployed the XB-X - for good this time!
Over two weeks later, it's still floating just as it should. The electronics are blinking away! I'm pumped. The satellite telemetry isn't behaving exactly how I thought, so that's the focus for the first block of upgrades this week.
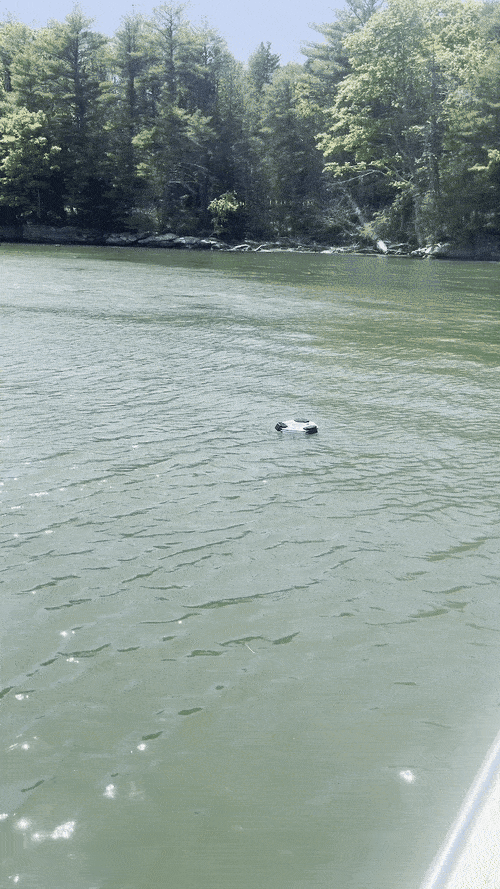
May 26th - June 1st
Almost Entirely Written Off
My brother graduated over the weekend and we had a lot of family in town visiting. I took off several days to celebrate. Over graduation I caught some kind of sickness and that kept me out of commission until the following week.
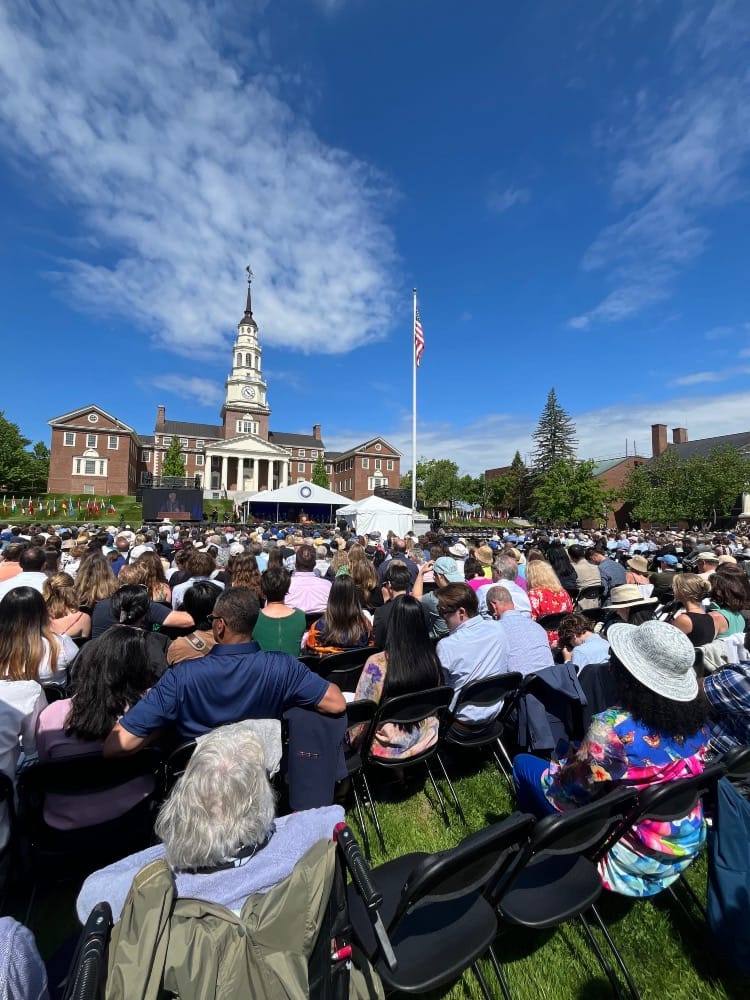
June 2nd - June 8th
DB-X Push Week
Since the beginning of May I've been working on prepping all the individual components needed to build the first batch of DB-X buoys. It's kept me pretty busy, but this was the big tie it all together week.
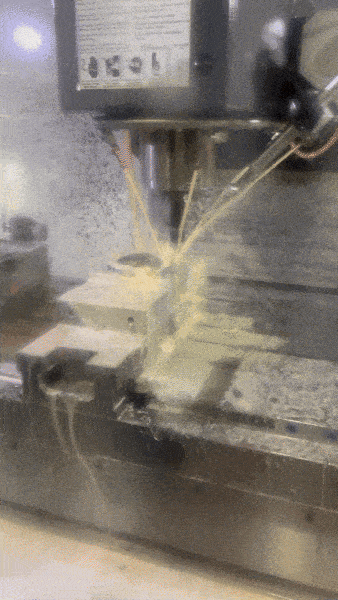
I finished printing the last of the internal sleeves and top caps (the last two top caps are actually still on the printer now, but will finish by Monday morning).
I went to go start assembling full buoys on Wednesday before discovering a couple issues with a set of the 3D printed sleeves. 110051 is one of the 3 unique internal sleeve parts in each DB-X. Each DB-X contains 3 of them, so in total I made a little over 30. The problem being every single part was slightly oversized - enough I couldn't just sand it to fit, or mash it in. I went home on Wednesday night super defeated and worried this would be catastrophic and set me back - probably over a week and $100 worth of filament if I had to guess.
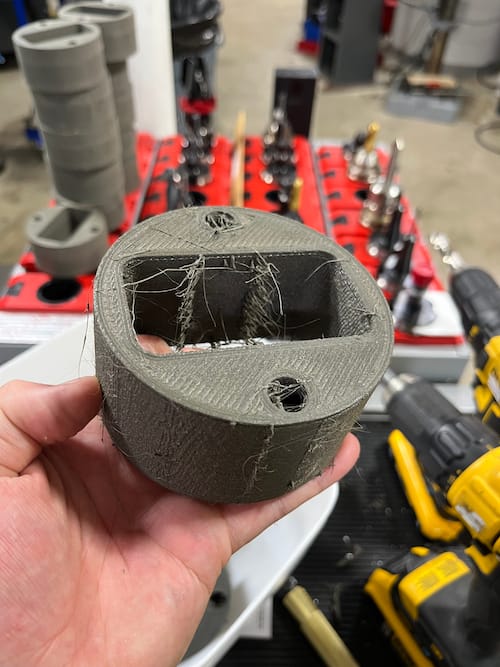
I thought over the problem on the couch at home, watching James May explore the wonderful world of Japan. There's irony in there somewhere because Toyota is Japanese and they have a phenomenal engineering/manufacturing framework and philosophy that if I'd practiced more thoroughly, would've prevented this issue entirely. Alas.
With some advice, guidance and war stories from others at the shop, I settled on trying to post-machine my 3D prints. Andy, I don't know what the hell post-machining is, use real people words. My bad... So, usually you 3D print something, and it might be good enough as it is. Sometimes you might sand it to make the surfaces look cleaner/smoother/more uniform. You might even paint it or coat it with another material. These all fall into the bucket of post-processing. Another post-processing step would be machining - where you put the 3D printed part back into a mill of some sort, and remove material with an end-mill or drill bit.

I don't think this is particularly unique, rare, or revolutionary. I've just never done it before, and had no idea how it was gonna go. When you're on all sorts of time and budget constraints, venturing this far into the unknown can get stressful. The parts as printed were pretty solid, but I was worried they'd shatter into a million pieces during machining. All that worry for not though, the whole process went super smoothly.
The 110051 - SLEEVE has an outer diameter, a rectangular pass-through on the inside for the battery, and two alignment holes. I designed and machined a jig for the CNC mill that let me align and bolt down each sleeve. Then the machine would remove material from the outside and inside, bringing the part back into spec - it looked and fit perfectly!
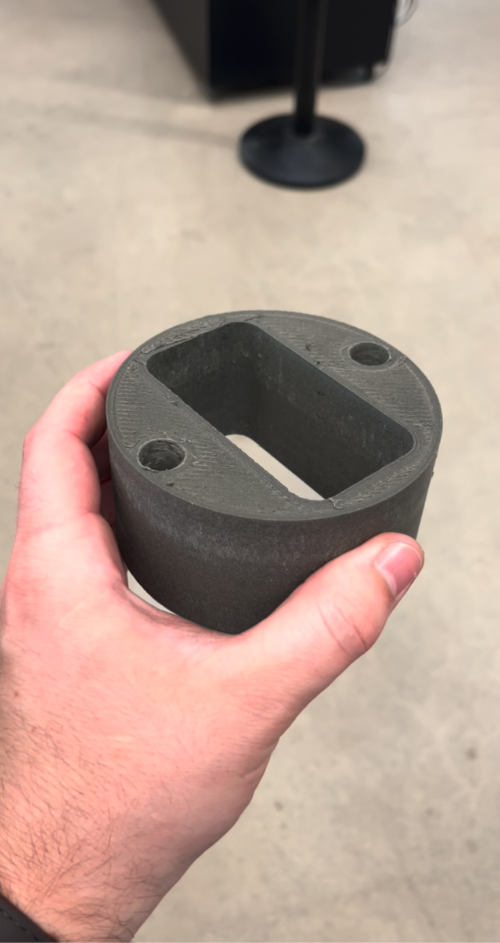
With that fire put out, I was able to proceed with final assembly without any issues! I installed all the sleeves, bonded on the end caps, cleaned up the body tubes and assembled all of the electronics stacks on Friday.
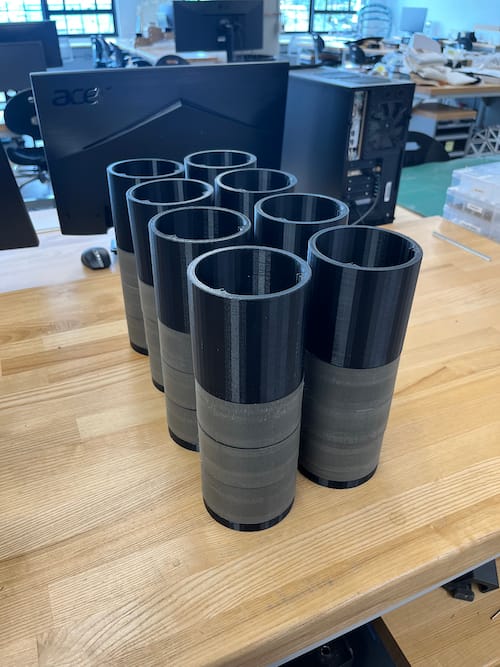
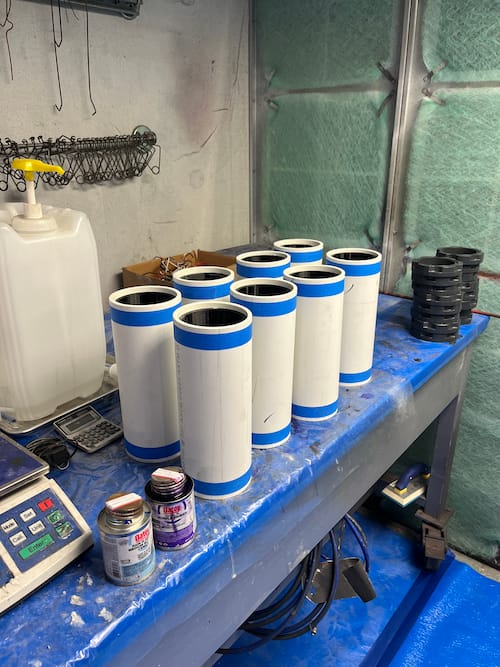
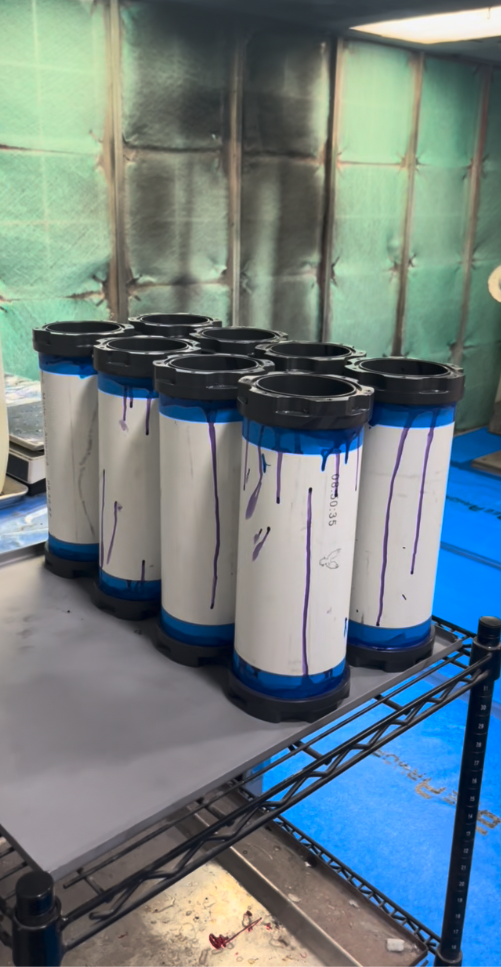
DB-X sleeves and end cap assembly
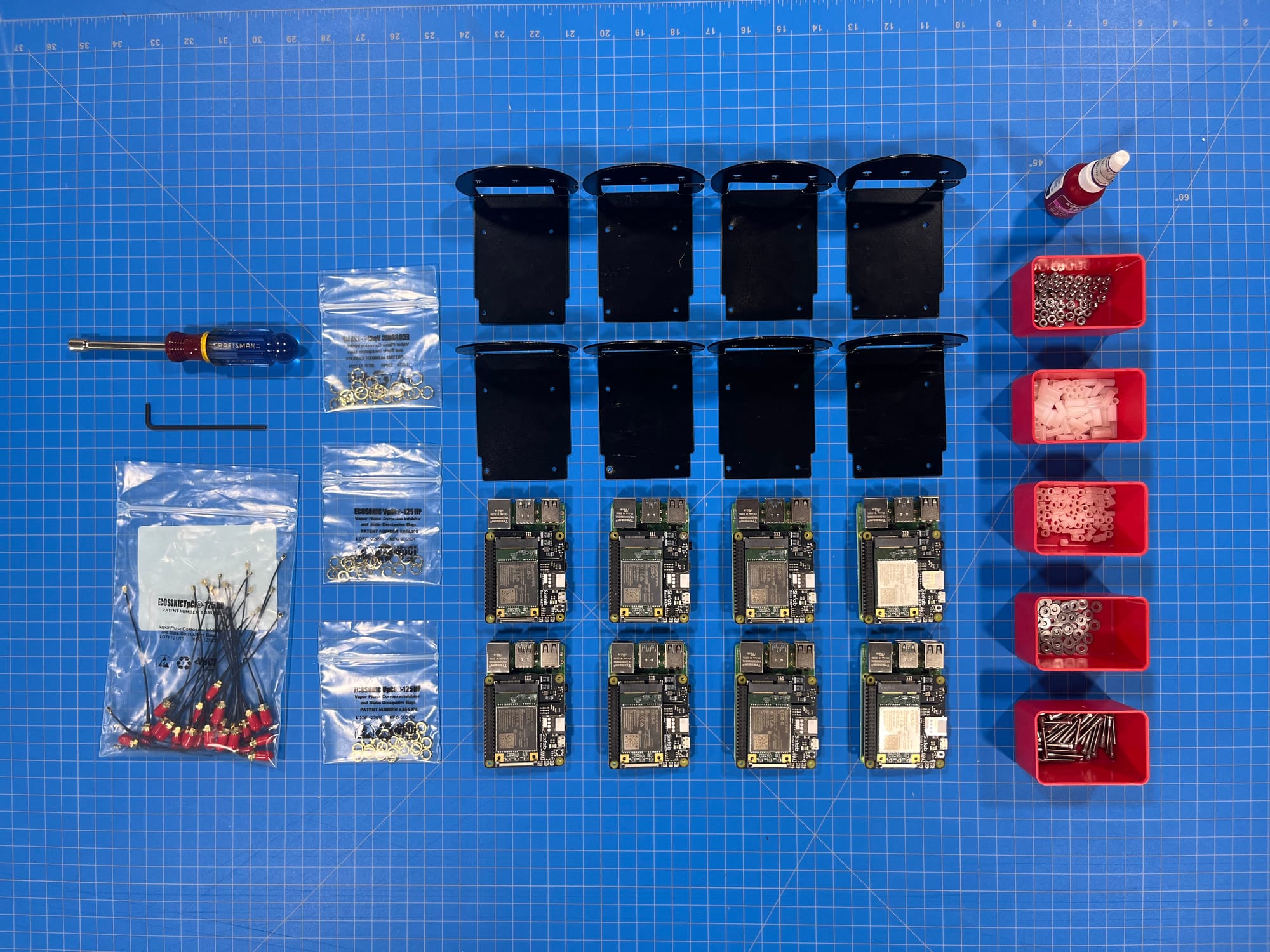
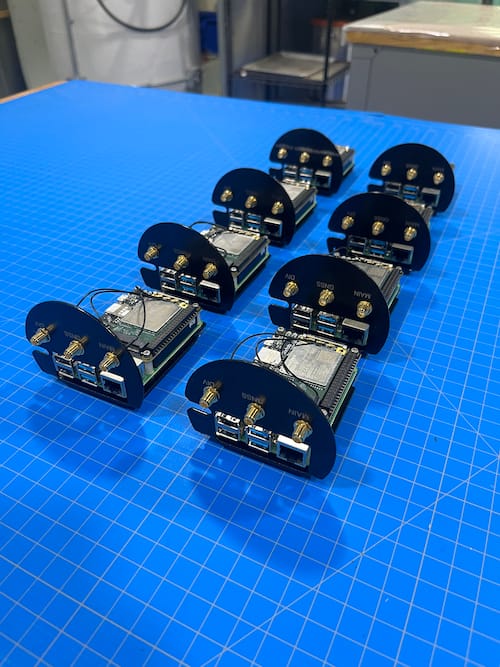
DB-X electronics stacks
I have the last couple of 3D printed parts still printing, but it's all looking good for a delivery next week!
Next Week
DB-X Delivery
Plan right now is to wrap up final assembly and fabrication on Monday before delivering them in person on Tuesday.
DB-X Software
The software is in a pretty solid spot now after spending a pretty big chunk of time on it yesterday. The whole telemetry system is based on MQTT and I have two way communications/functionality all ironed out.
I think the complete software rewrite was a good call. The architecture is nothing like what it was, and now it's a lot more configurable, and extensible later.
XB-X Upgrades
Max and Ferda Farms have had their first XB-X deployed for a couple weeks now. Like I mentioned above, there are some upgrades I'd like to roll out over time on top of delivery additional buoys.
First upgrade is telemetry. I won't get into the whole trade study, but the XB-X originally had a satellite radio. After all the success of the cellular radio in the DB-X I'm going to bring that to the XB-X.
Second upgrade is in the hull/electronics mounting mechanism. This one bums me out a little. I spent soooo much time developing the latches and clasps to hold the buoy and electronics enclosure firmly together. During assembly of the last XB-X, with the standoff to secure the ballast weight, I realized there's a super easy and obvious way to build a second standoff that could tie everything together. Sunk cost fallacy is real, and it's hard to let go of my latch efforts, but this is a much better way to go.
I'd like to have this all rolled out for another deployment at Ferda on Friday or Saturday, but we'll see how DB-X delivery goes first.
Online Store
Not a crazy high priority, but with DB-X and XB-X both in pretty good places, I want to get the store ironed out. I want to sell company merch, but more importantly I need an outlet to sell actual devices, which I'm now ready for now at this point!
Wins
New Brakes
I have new brakes on my truck now. They no longer squeak. Everyone likes working brakes I think.
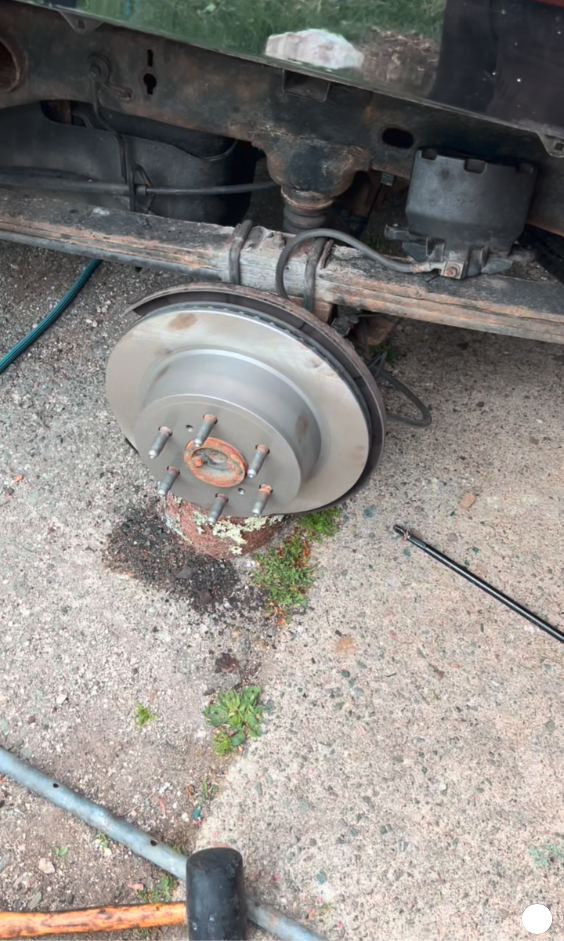
Fantasy Baseball
Leading the league right now, 6-3-0, staring down the barrel of another win right now. I cleaned up my corner infield and moved through a couple of catchers. Offense still isn't insanely strong, but definitely workable!
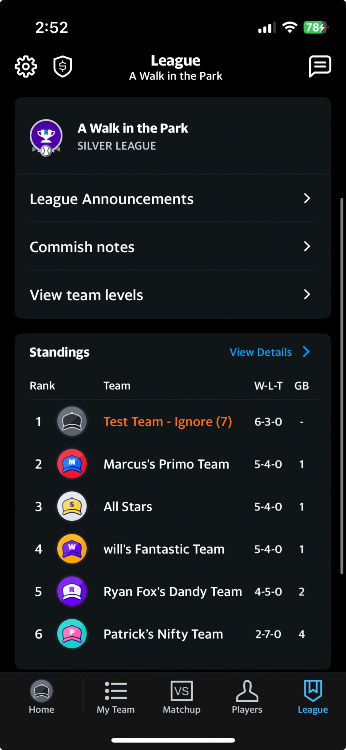
Losses
New Brakes
Truck fell off the jack while I was finish up on one of the new brake rotors. Not fun getting that guy back on four tires...
Checo
Buddy... Two Q1 exits in a row is not a good look on a new contract...
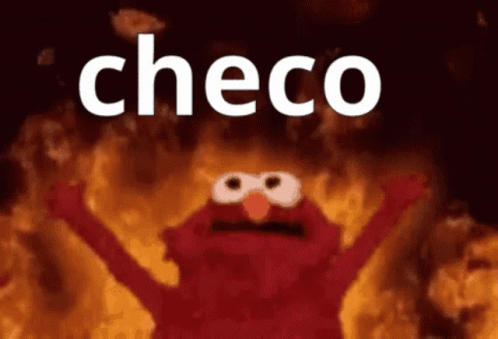
Closing Monologue
Stay tuned for another (on time) Captains Log entry next weekend-ish some time. The weather is looking absolutely stunning here in Boston. I'm desperately looking forward to walking, running, biking in the sun next week, you should do the same!
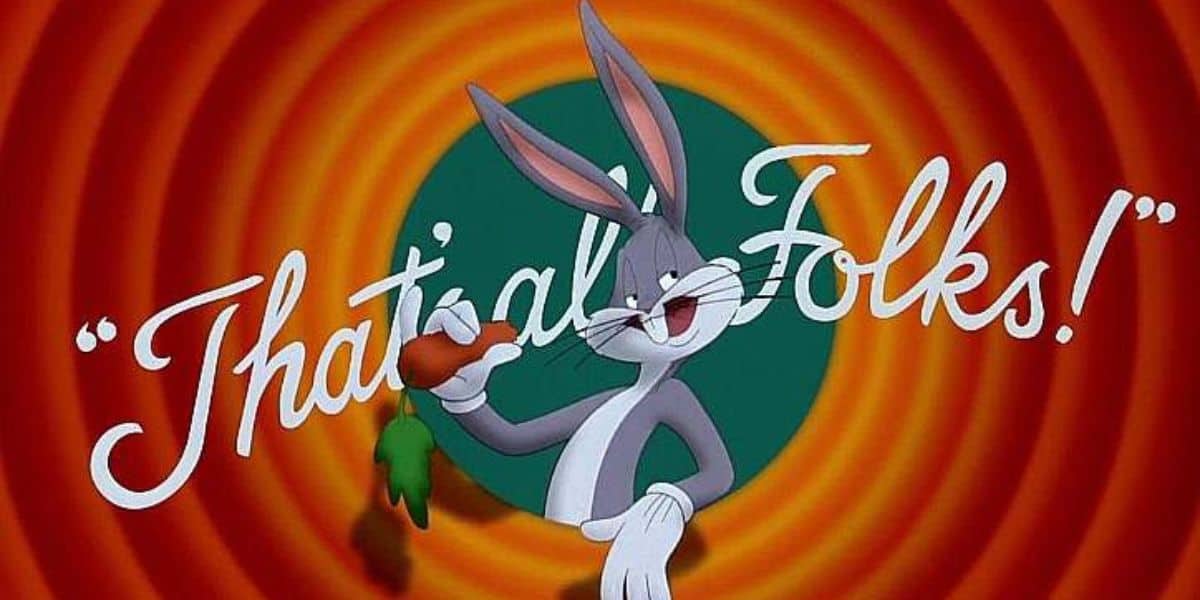