My favorite planet is the sun.
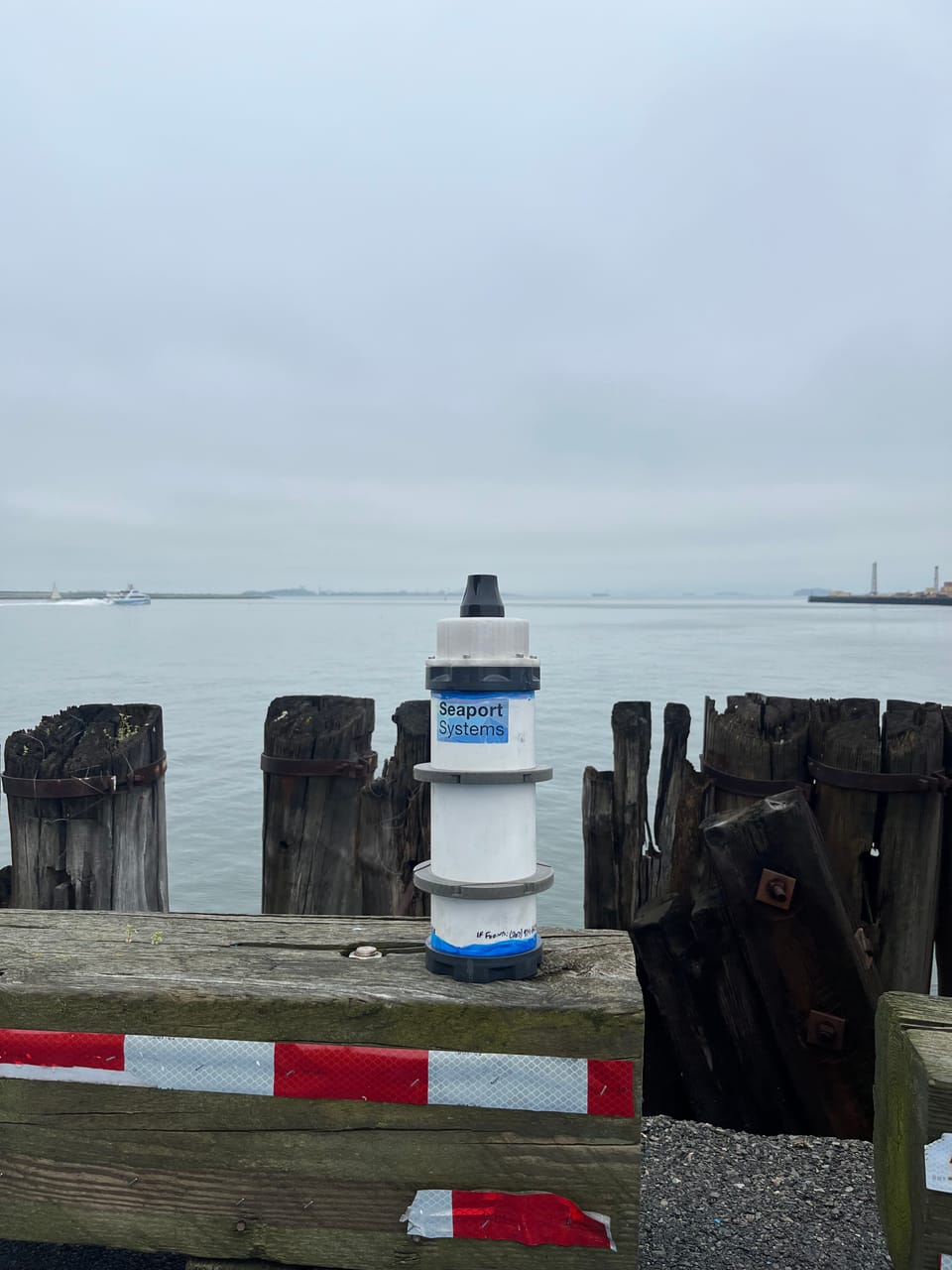
Welcome back to the Captain's Log!
I had some interesting back and forth with folks about the last post, over the course of the week. A couple of people really like the production vs. progression framework; a few people had varying levels of disagreement (definitely agree there are some holes); and a few people had good thoughts that I think will help me write more effectively about stuff like that in the future!
Opening Monologue
I opened last week saying that it was definitely a prep week, setting up this week to be more productive. I definitely felt that! I checked a lot off the to-do list, but at the same time, I also feel like I've done a good amount of work to enable next week. It feels like I'm in Guitar Hero or Dance Dance Revolution where you start off with a 1x multiplier, then you get a 2x, 3x and 4x. So I've got inertia right now, we're rockin' out, got a cool 2x multiplier. Hopefully Star Power can help me close out the first order of DB-X buoys, and finally getting Ferda Farms connected with XB-X buoys!
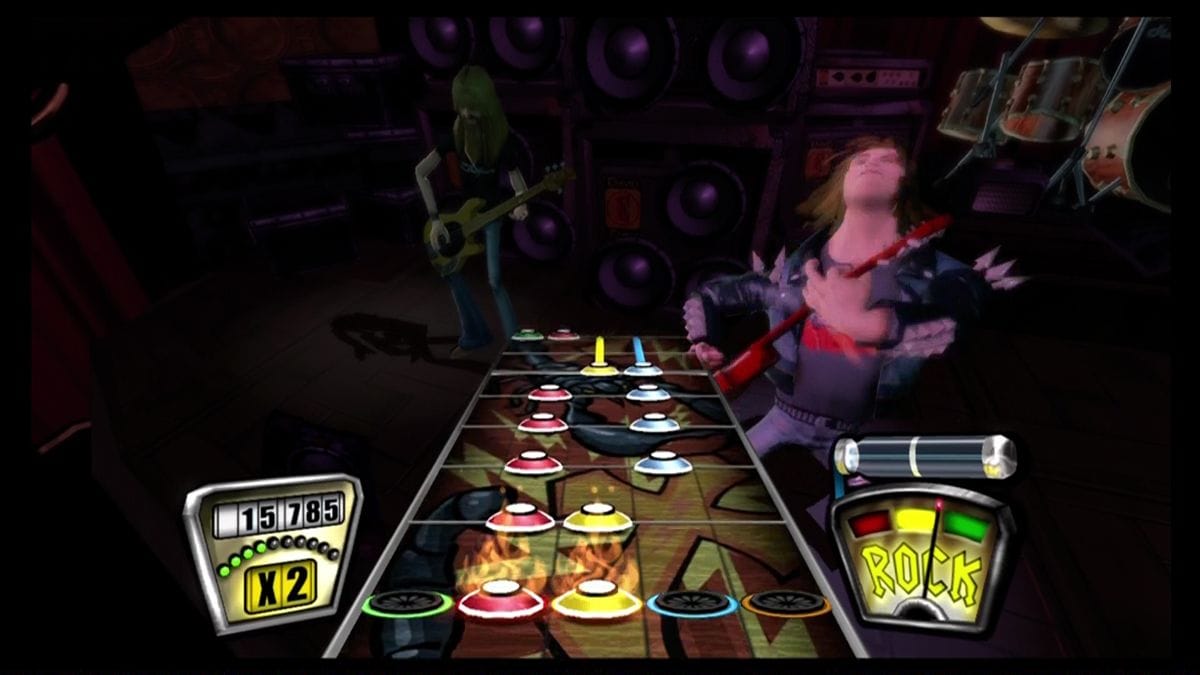
Perfectionism, or avoiding it rather, has been really front of mind for me this week. I'm closer than ever to having the XB-X buoys ready for Ferda Farms, but it seems like every time I get close, there's something I want to change or make better.
Last year, my goal was to get hardware out the door as quick as possible, even if it was pretty rough around the edges. That strategy worked for a bit, but unfortunately, the pencil wasn't quite sharp enough and so nothing went together quite right. The buoys literally melted in my truck, and the hole patterns for the electronics housings weren't even close to lining up. I was 12 hours away from the scheduled deployment date and I had damn near a mental break on the bank of the Charles River. The geese did not help, if that's a surprise to anyone...
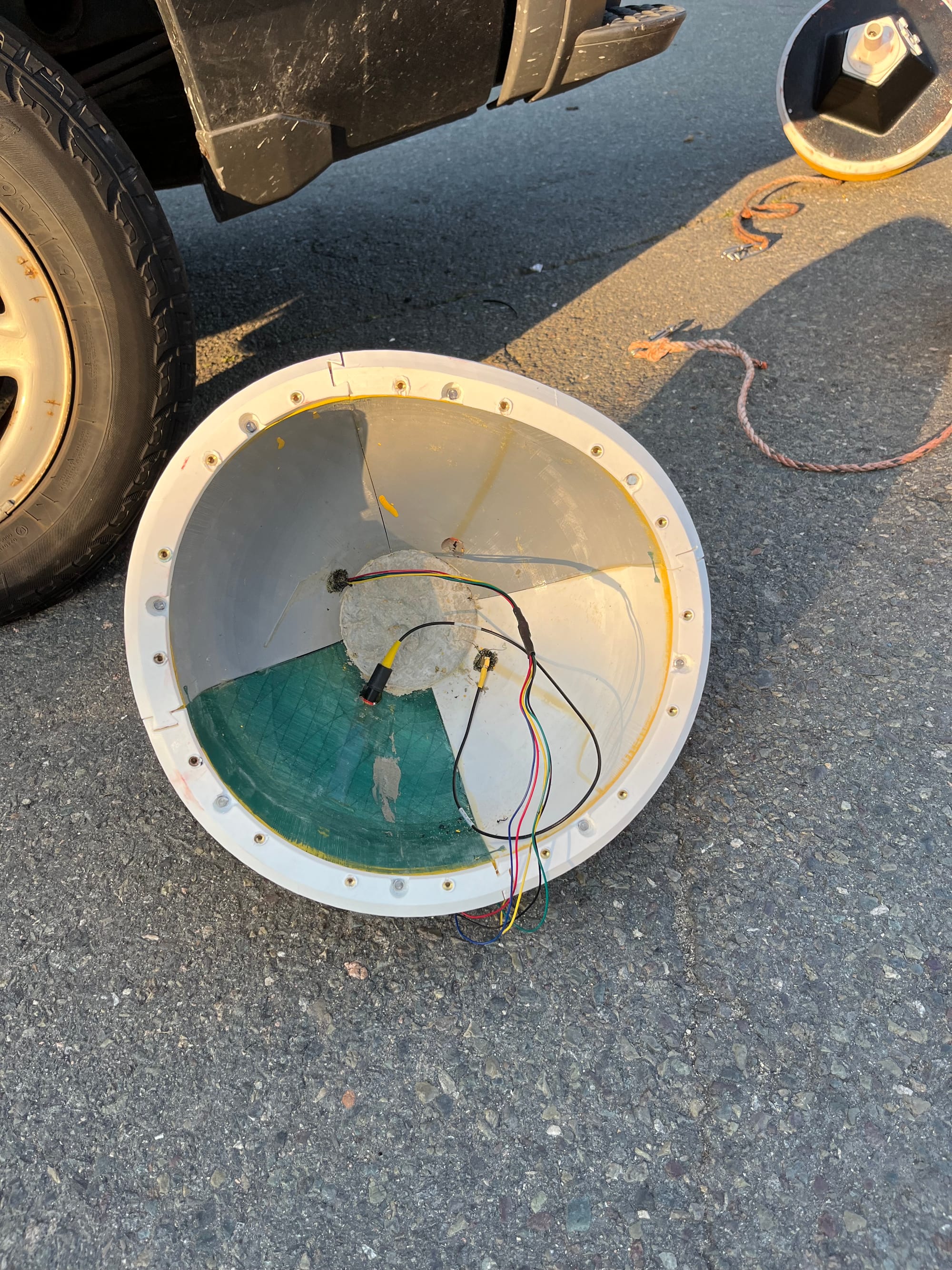
I wiffed pretty hard on deploying then, and so I spent the winter and spring over-correcting from the quick, hacked together MVP (minimum viable product). I'd argue that over-correction and over-building is drastically better than under-correcting and running into the same problems over and over again. None of that matters though, if you never ship anything.
I've caught myself several times this week where I wanted to over-build or over-engineer parts of the XB-X at the cost of another week in the shop machining and fabricating. Rivers, lakes and oceans are amongst the most brutal environments to design for and they will punish and abuse anything you throw at them. Seeing some of the first buoys take on water was petrifying and so I'm insanely paranoid something bad will happen again. But I don't think I have to be. Like I said, I've already re-designed the hulls and electronics enclosures. Hopefully without jinxing myself, everything valuable is safe. If the hull takes on some water, the electronics enclosure is entirely buoyant by itself. The seals are insanely simple and as bulletproof as they can be. Even if something catastrophic does happen, it's a prototype.
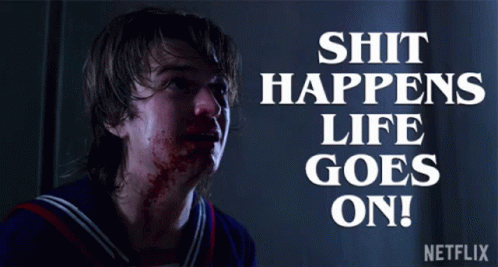
I doubt these 3 XB-X buoys will be the same at the end of the season anyway! 2 weeks after they hit the water, I'm sure I'll want to change something. I'll make new parts, and swap them out. Maybe a week after that something else breaks. New parts, swap them out. 3 weeks later, the oyster farmer wants to mount it to their gear differently. New parts, swap them out!
I never addressed learning by experience in my rant last week. It's certainly worth exploring in the future, but for the record, I completely recognize that what I'm about to say conflicts entirely with last week's blog. There's no way to learn what part of the buoy's design needs to be changed, fixed, or redone entirely without deploying them first. That's been my fatal flaw in the XB-X's development.
Moral of the story is, many of this week's updates are non-updates. They're things I've decided not to do, because they don't need to be done yet.
This Week
T-Shirts
Insanely ironic I close the opening monologue saying I've ixnayed a bunch of stuff that isn't important, just to write something about company merch...
Absolutely mint, thanks Zack!
I will justify my actions by saying two things:
- I was running out of clothes, and I've gaslit myself into believing that making Seaport Systems merch was the fastest, cheapest (and tax-free) way to having more than 3 shirts.
- I have spent less than 1 hour a week on this over the last 2 months. I'm not spending any considerable amount of time on this. When I do, it's almost always while I'm at home watching TV at night.
The update then, is I put together a little photo shoot over lunch on Monday with my buddy Zack, of machine shop fame. We spent a few minutes getting some shots for the 'gram and the website for whenever I got around to launching. The photos came out amazing, he's a natural. I have no doubt that Summit Racing, Carhartt, and LLBean will be fighting over this dapper fella for their fall catalogs.
Electronics Housings
This is a prime example of the public outcry/accountability I wanted when I started the blog. I felt immensely guilty writing for the third week in a row that I needed to do a critical thing. I also had several people reach out and shame me directly. Thank you!
On Monday I glued the MDF sheets together to make the big chunk of material I needed for the mold.
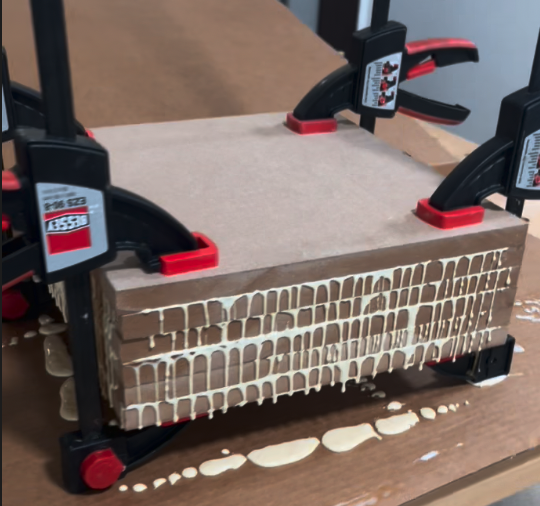
I've had someone else at the shop mill most of my molds on the gargantuan 5-axis router downstairs, but this one was small enough to fit on a smaller 3-axis router. I'd never run this specific machine before, so I think that was the big mental hurdle for me to get over for this project.
On Tuesday afternoon I got the block trimmed up, and mounted on the machine. Even with a quick crash course on setting up and running the machine, the whole process took less than 2 hours!
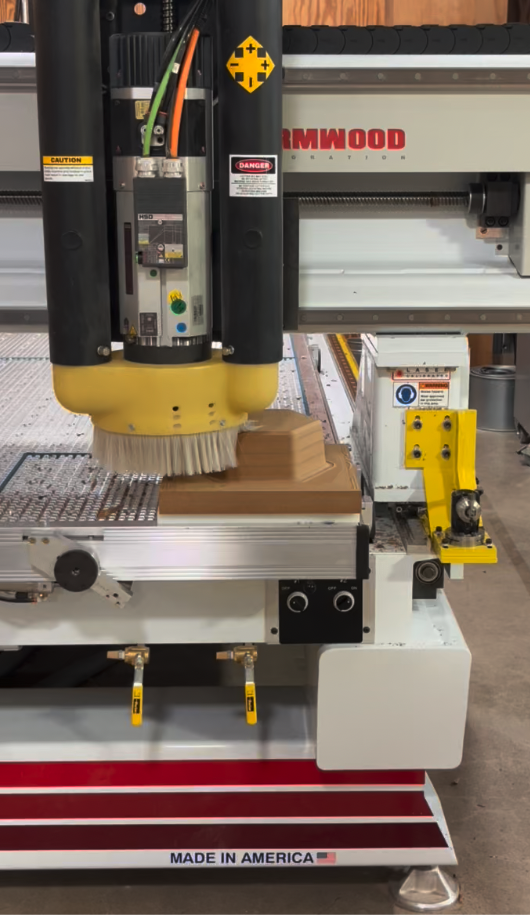
Vacuum forming after getting the new mold didn't quite go as planned. I was trying to use some small scrap pieces I had left over, but they weren't quite big enough to generate a vacuum seal. I'll get some properly sized sheets in early next week, and we'll be wrapped with this saga entirely.
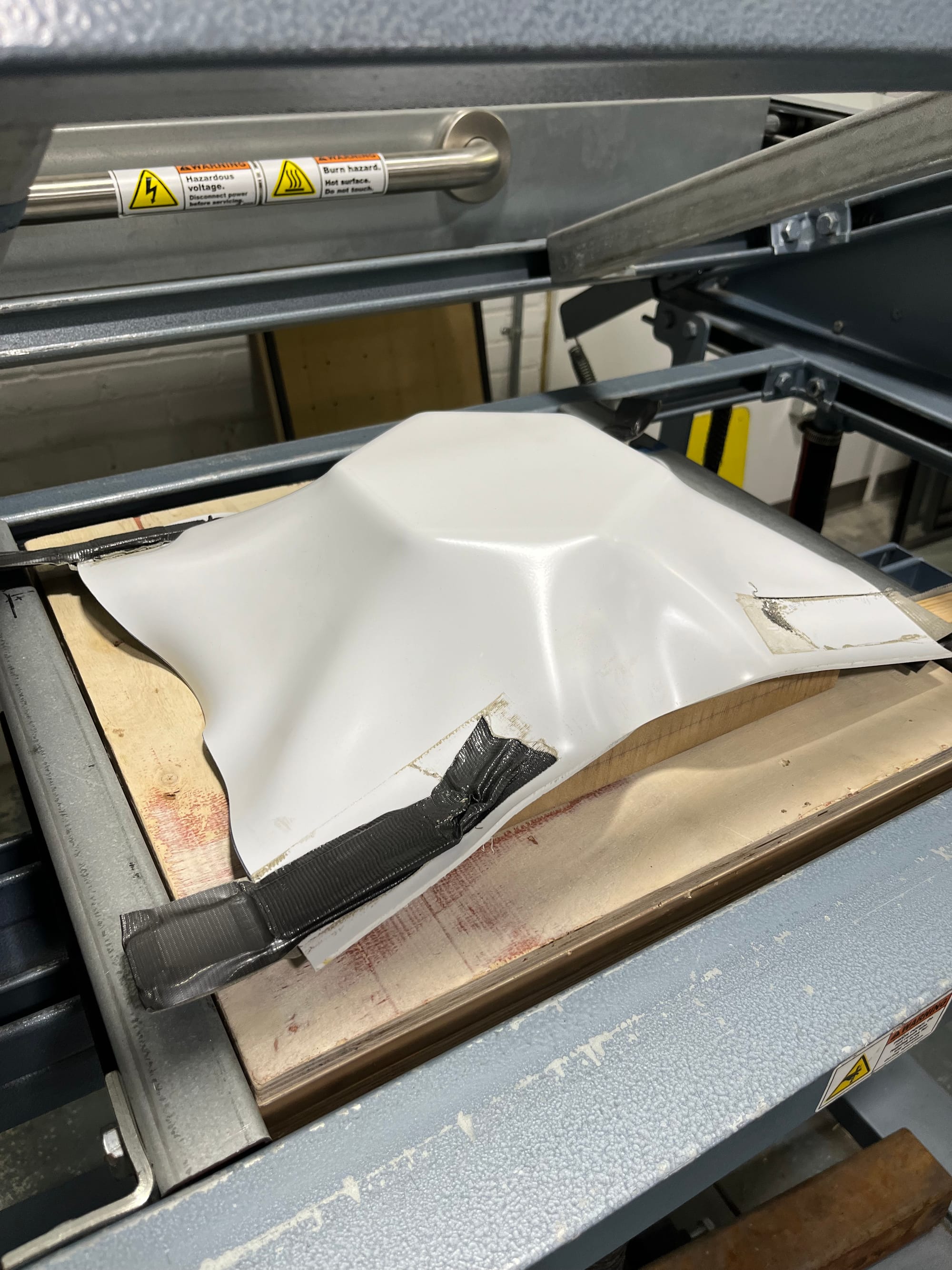
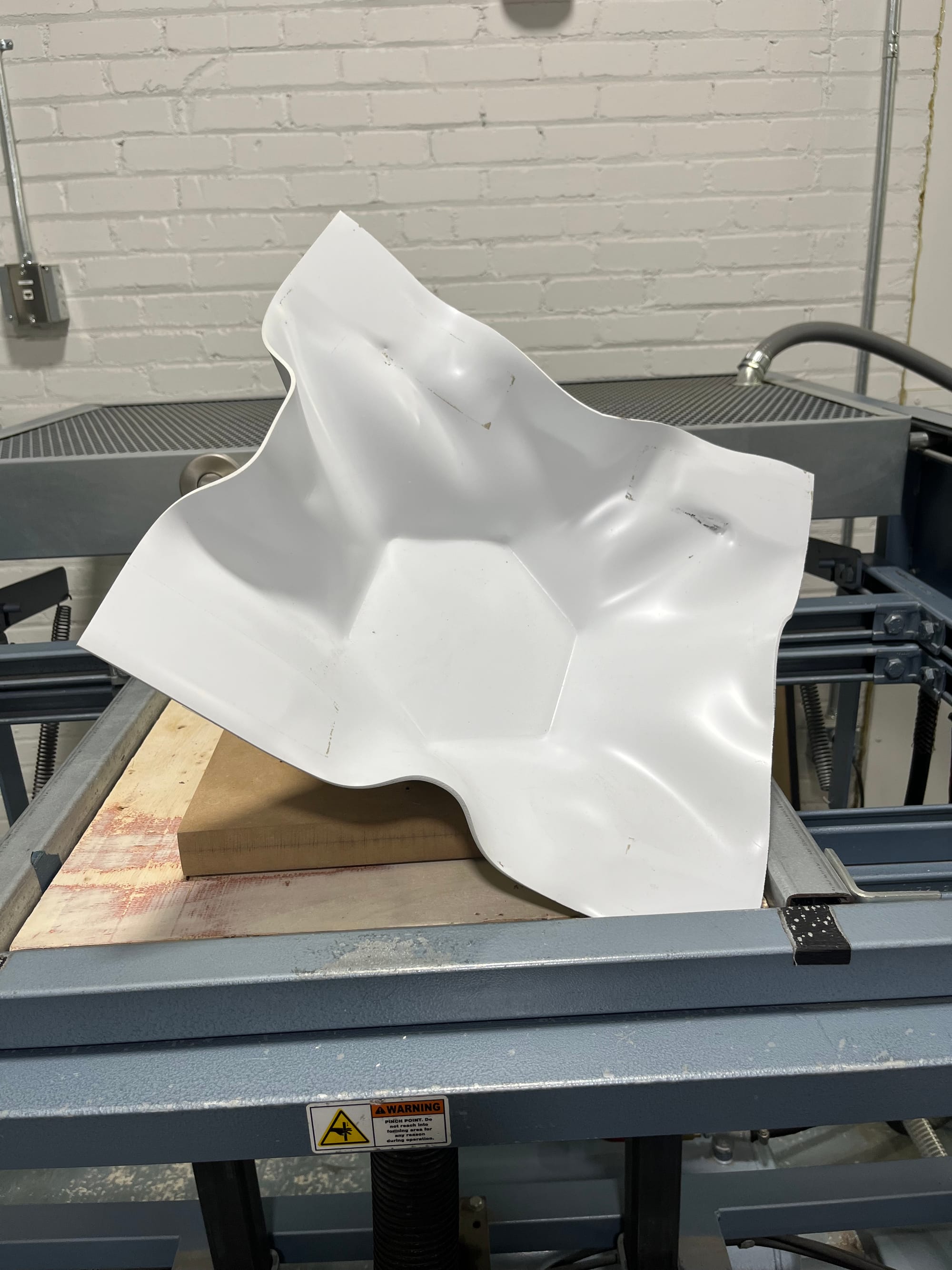
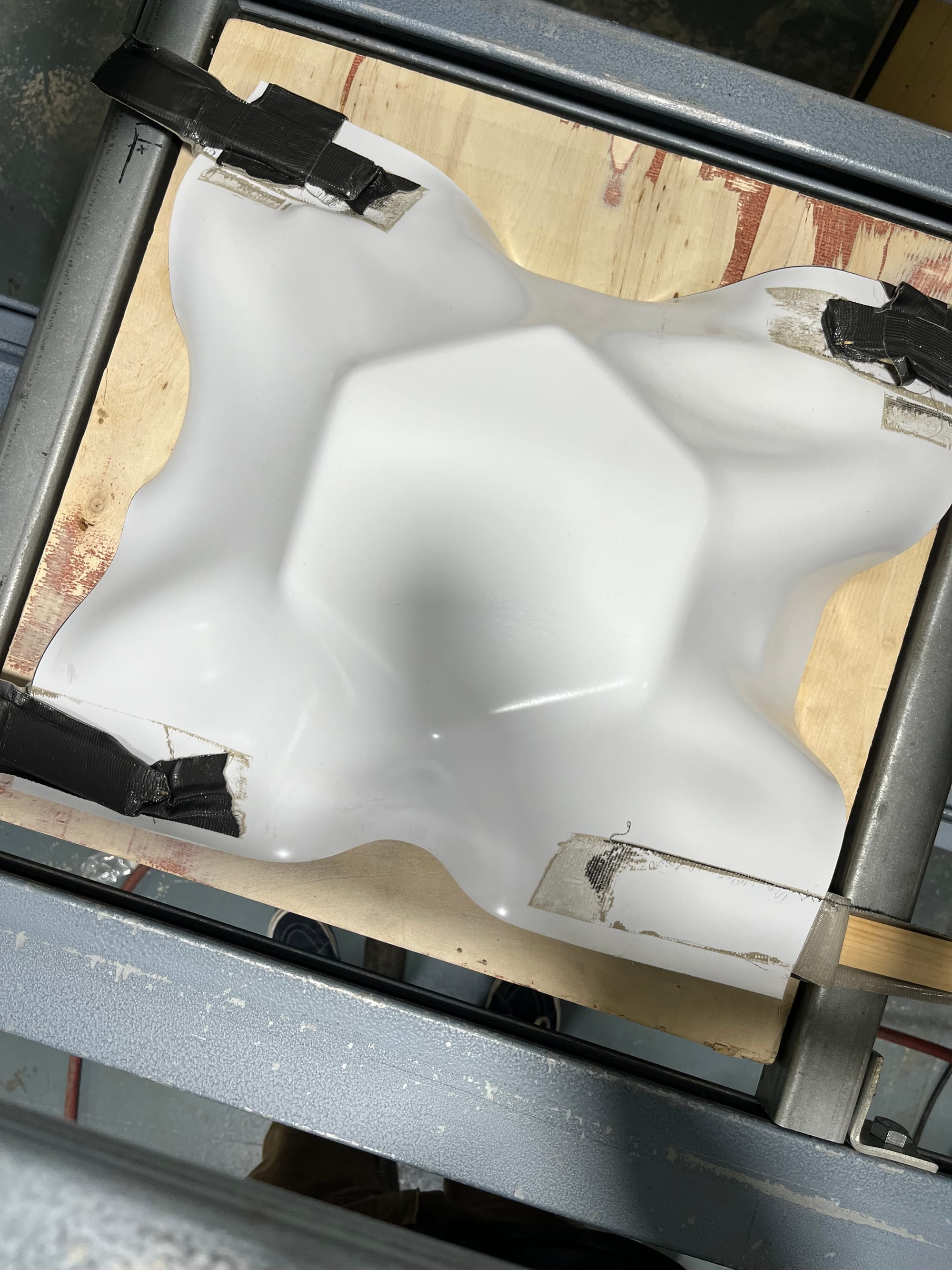
Andrew Vaughan Whitman, self-certified contemporary artist
XB-X Hull and Top Collar Drama
A few weeks ago, I dialed in the process of vacuum forming and popping the plastic hulls off their molds. I made a bunch of hulls, and they've been lying around ever since, but hadn't bothered test fitting them until this past Friday. The first test part fit great, but none of the parts from the second round of forming fit, they were all too small.
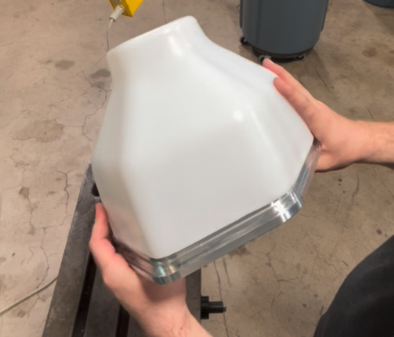
Everything I'm aware of expands when it gets hot, and contracts when it gets cold. I'm almost positive that what has happened is during the first test part, the plastic was able to cool for probably 45-60 minutes on the MDF mold before I could pry it off. It shrunk back as far as it could, but with the mold still in the way, it could only shrink down to the size of the mold.
During the subsequent run of parts, I waited maybe 10 to 15 minutes for the plastic to firm up, but I took the part off the model after that. Without the mold, the plastic part was able to contract unrestricted, and now they're all undersized.
I was able to get setup pretty quickly to remove material from the top collar. I almost got stuck in a loop trying to dive too deep into the issue, when all that really mattered was getting the parts to fit for now. That way they can be deployed in the next week or two. Once they're deployed, there's all the time in the world to figure out precisely what happened and how to prevent it from happening again.
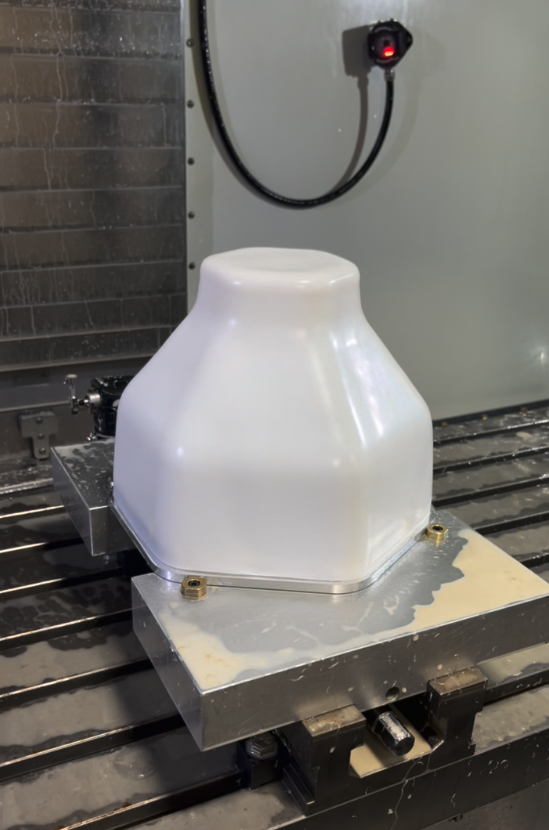
XB-X Probe Ports
The point of environmental monitoring buoys is to monitor the environment, obviously. We need probes to do that, and they protrude from the hull.
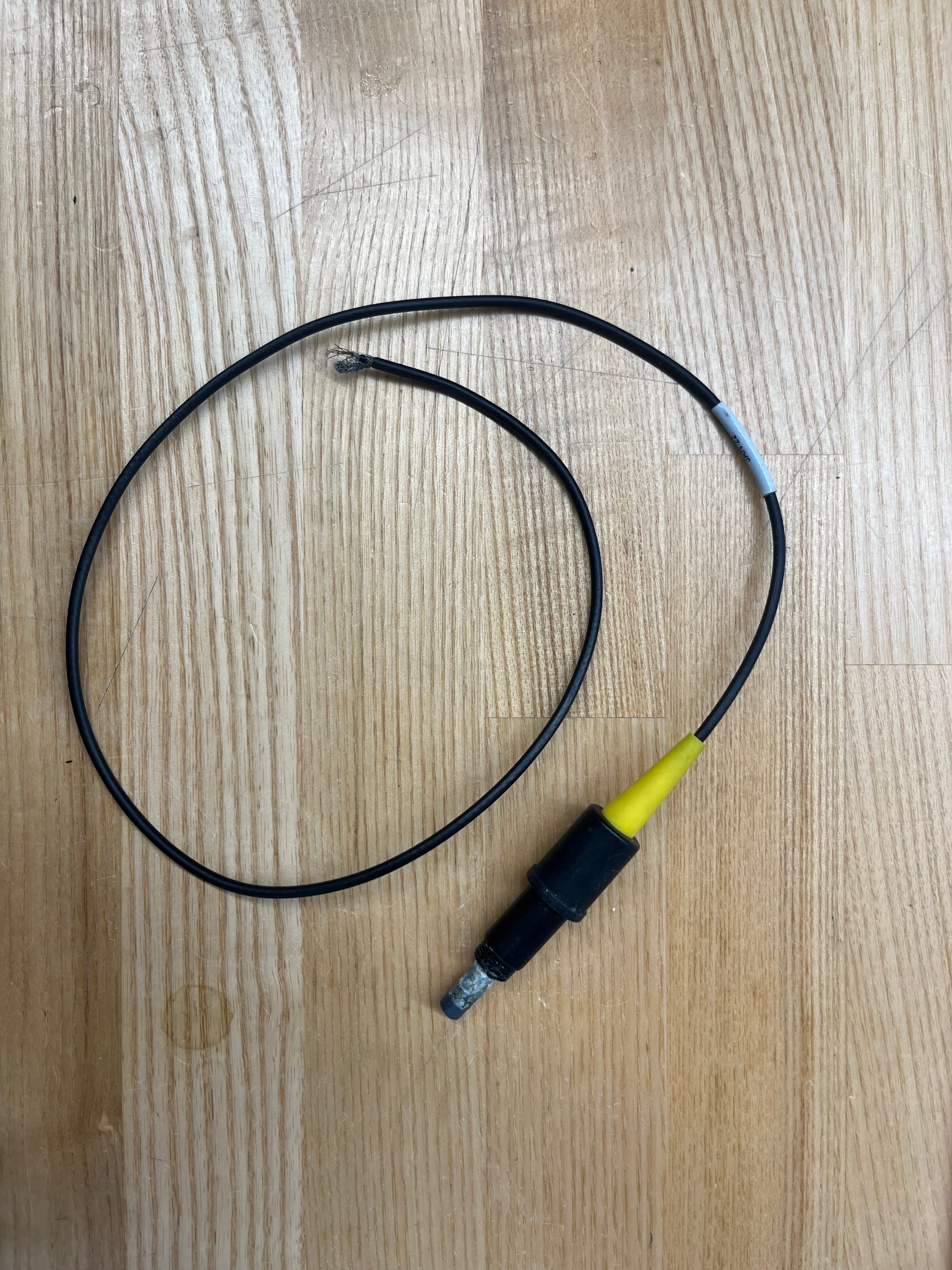
The ports I'd need to make are the last piece of design work to do for the XB-X. I've been putting it off because I feel the need to over engineer the solution. Before designing much, or even thinking about machining, I stopped myself.
I want the ports to be standard across all the buoys I end up making. I want the interface to be simple and robust. I want a lot of things, but right now all I need is for the XB-X buoys to have probes, and for those probes to mostly not leak.
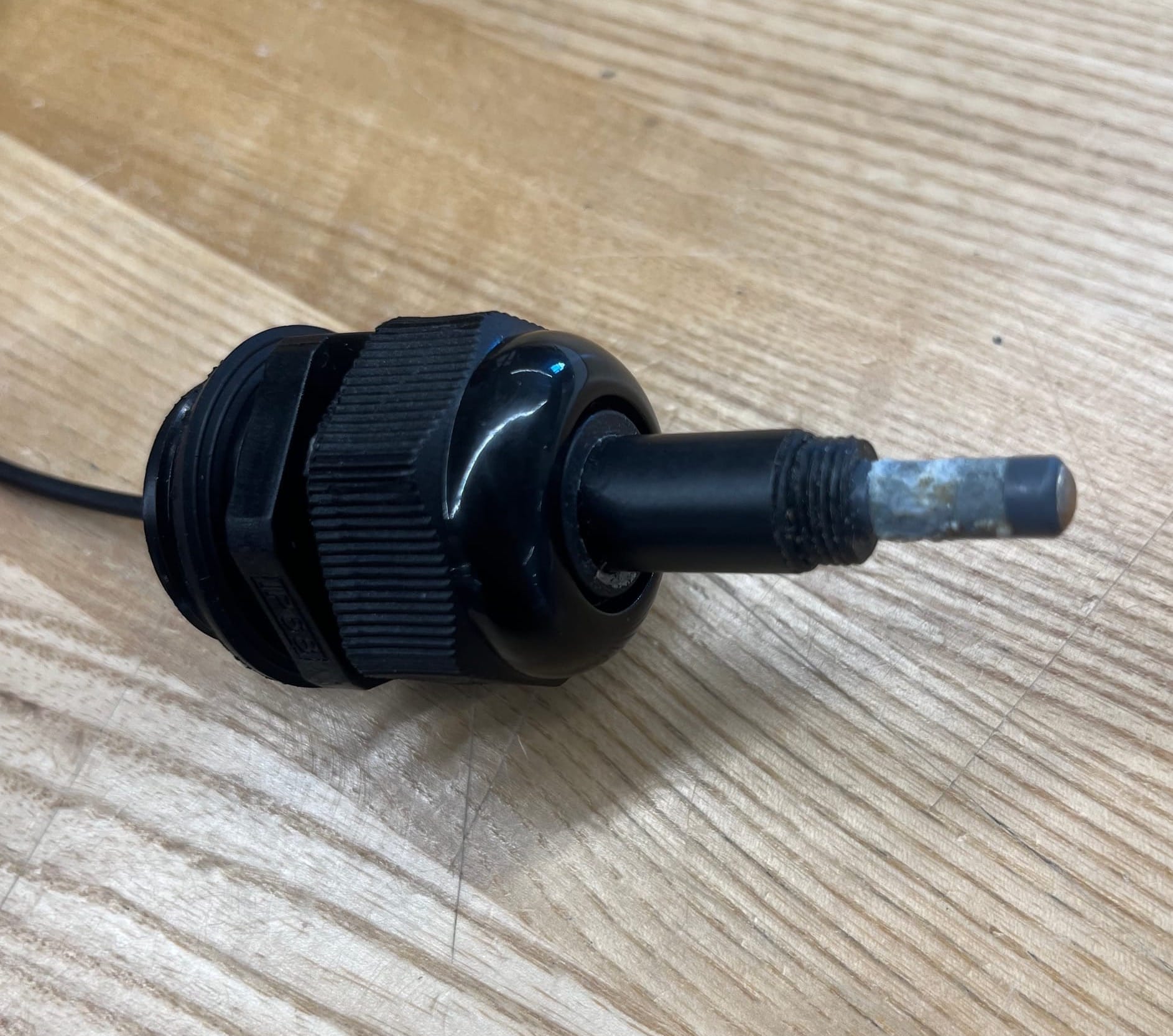
After drastically over-simplifying the problem, I decided that cable gland seals would more than do the trick for the first three buoys. Cable glands are pretty slick. They're basically a nut that threads on to a hollow fitting. A cable, or in my case sensor probe, slides through the hollow fitting. As you tighten the nut, it forces a rubber gland to shrink around your cable, effectively creating a water-tight seal.
Instead of a week long prototyping campaign, I was able to order 1 part on McMaster-Carr and solve my problem for the time being...
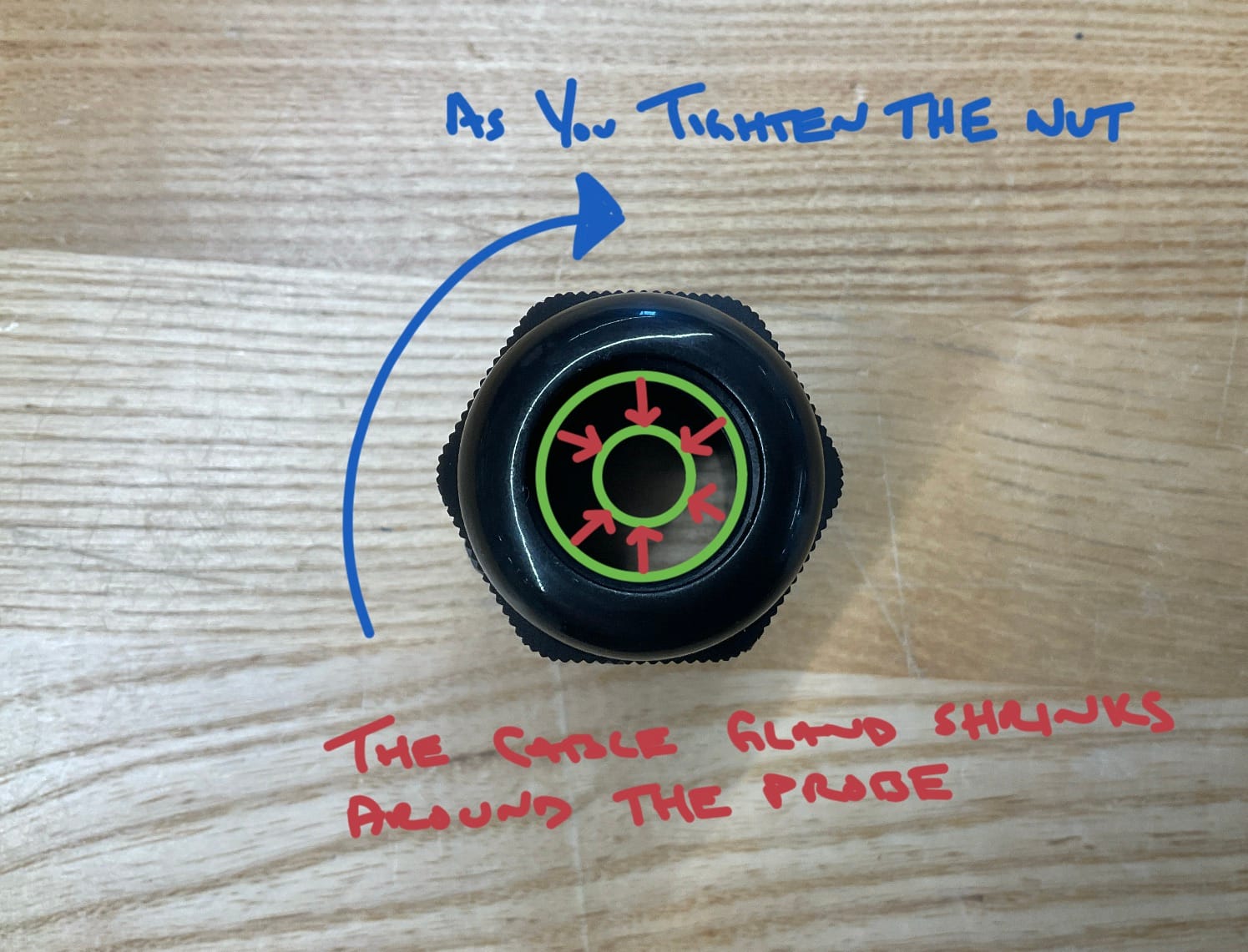
Material/Stock Prep
I think most of my time next week will be spent in the machine shop. In garbage time on Friday, I diced up a few blocks of aluminum into smaller more manageable pieces. I've got stock cut for DB-X and XB-X ballast parts. This way, I should be able to come in Monday morning and start cutting chips.
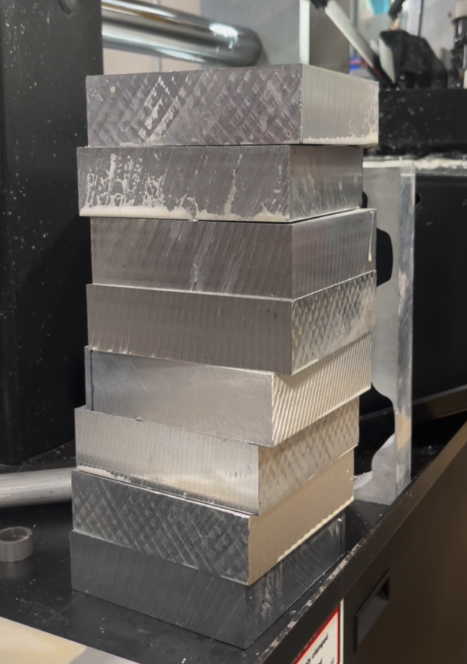
XB-X Latches
Another quick example of punting perfect solutions for later. After many dozens of prototypes, geometry and material selection is all sorted out for the XB-X latches. They can get a mid-summer refresh, but for now the design is good enough. I'll put 18 sets of latch parts on the 3D print queue, and forget about it.
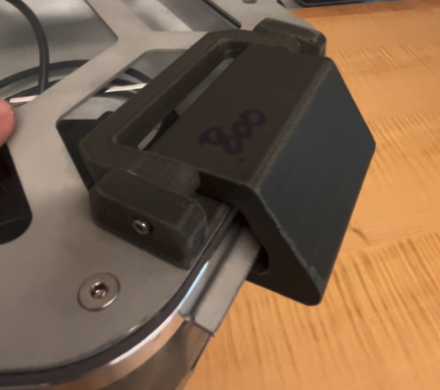
Next Week
DB-X Software
After a set of completely successful tests over the last few weeks, the DB-X software doesn't seem to work... I'm sure I've done something to awake the ghost in the machine, but alas.
I've been meaning to refactor the code for a while, but I think it's finally time. I'm on a sort of deadline to have the software all dialed in, so a complete re-write might be a little risky. Every actual software engineer is probably groaning right now. I guess you'll have to tune in next week for your "I told you so" moment, but hopefully I'll squeeze out a win here.
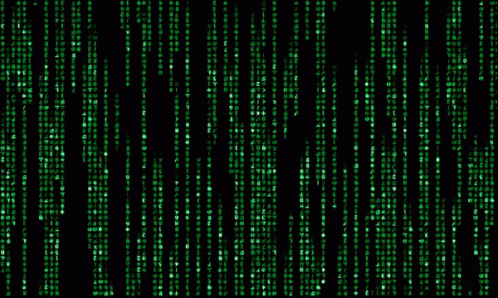
DB-X/XB-X Ballast Parts
The DB-X ballast is a cap that bolts on to the bottom of the buoy. Not only does it serve as ballast weight so that it sits properly in the water, but it helps seal the inside of the buoy from the water. It's gone through a couple of iterations, but I'm gearing up to machine 10 of the REV 003 ballasts.
- REV 001 - thin sheet metal part that only sealed the buoy, it didn't have much weight to it, the buoy did not float properly;
- REV 002 - 1.5 inch thick piece of aluminum, waterjet cut to have the cog profile of the end cap. It was a good weight, and got me through the first DB-X demos;
- REV 003 - nearly the same as 002, but now it's machined so it can slide into the end cap, reducing the overall length of the buoy, and adds a second, radial seal making the buoy more robust.
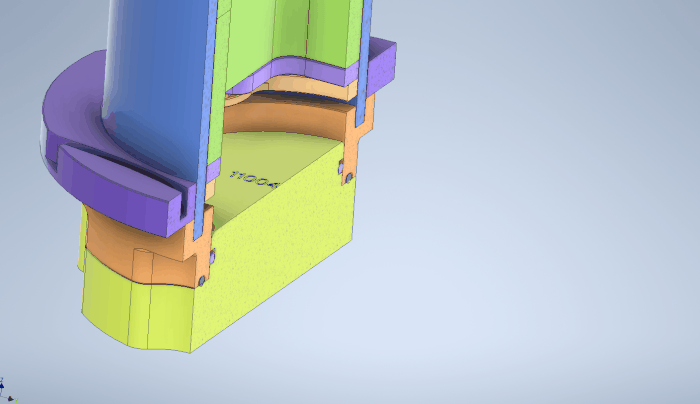
The XB-X ballast is actually more of a standoff mounted to the bottom of the inside of the hull. It provides a sturdy spot for the eyebolt to attach. The weight for the XB-X ballast actually comes from steel bead blasting media. It's far denser than Aluminum billet, it's cheaper than just about anything. Super simple solution. Another unnecessary over-engineered solution, simply avoided.
XB-X Final Assembly
I don't see anything preventing final assembly of the 3 Ferda Farms, XB-X buoys next week. I'm sure something will inevitably happen, but right now it's looking promising.
Wins
Clear Parts
Some of the first prototypes I've been doing lately have been out of clear PETG plastic. This is mainly because I had it lying around from a past project, but it's proven to be incredibly useful and something I'll continue to do in the future. Clear assemblies obviously allow you to see inside of them, which has the benefit of being able to diagnose issues, and observe how parts interface. Additionally, they can look super cool and are great visual aids when talking to people about whatever it is you've built.
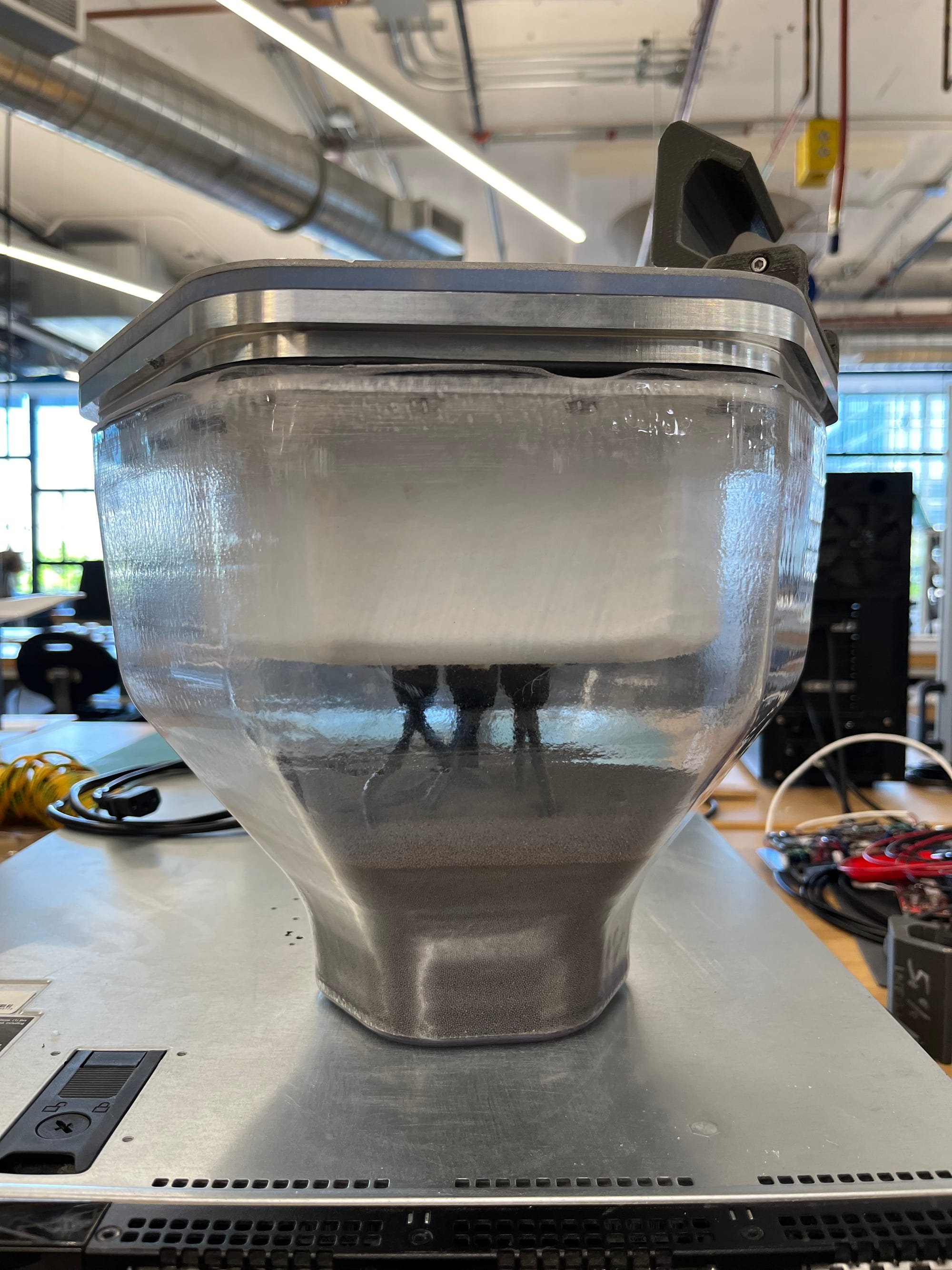
Focus
I've already covered over-engineering, under-engineering, etc... but I think focusing on what actually needs to be done immediately vs. what should get pushed for later has been something I've succeeded at this week.
Clarkson!!!
Clarkson and his farm are back. The first half of season 3 was out last Friday, the second half of the season came out last night. For those of you unfamiliar, boneheaded and slightly controversial car guru Jeremy Clarkson moves to the English countryside and starts tending to a farm. He realizes how hard it is and how every level of government is actively screwing farmers. He then uses his platform and takes to television to show the world. Absolutely hilarious, while still being awfully insightful. His most thoughtful work. 7/7 would recommend.

J. Cole
That's all I have to say.
Losses
Failed 3D Prints
Sometimes you know why they failed, other times you have absolutely no idea. Sometimes it's your fault, sometimes the machine just breaks. No matter what though, failed 3D prints suck.
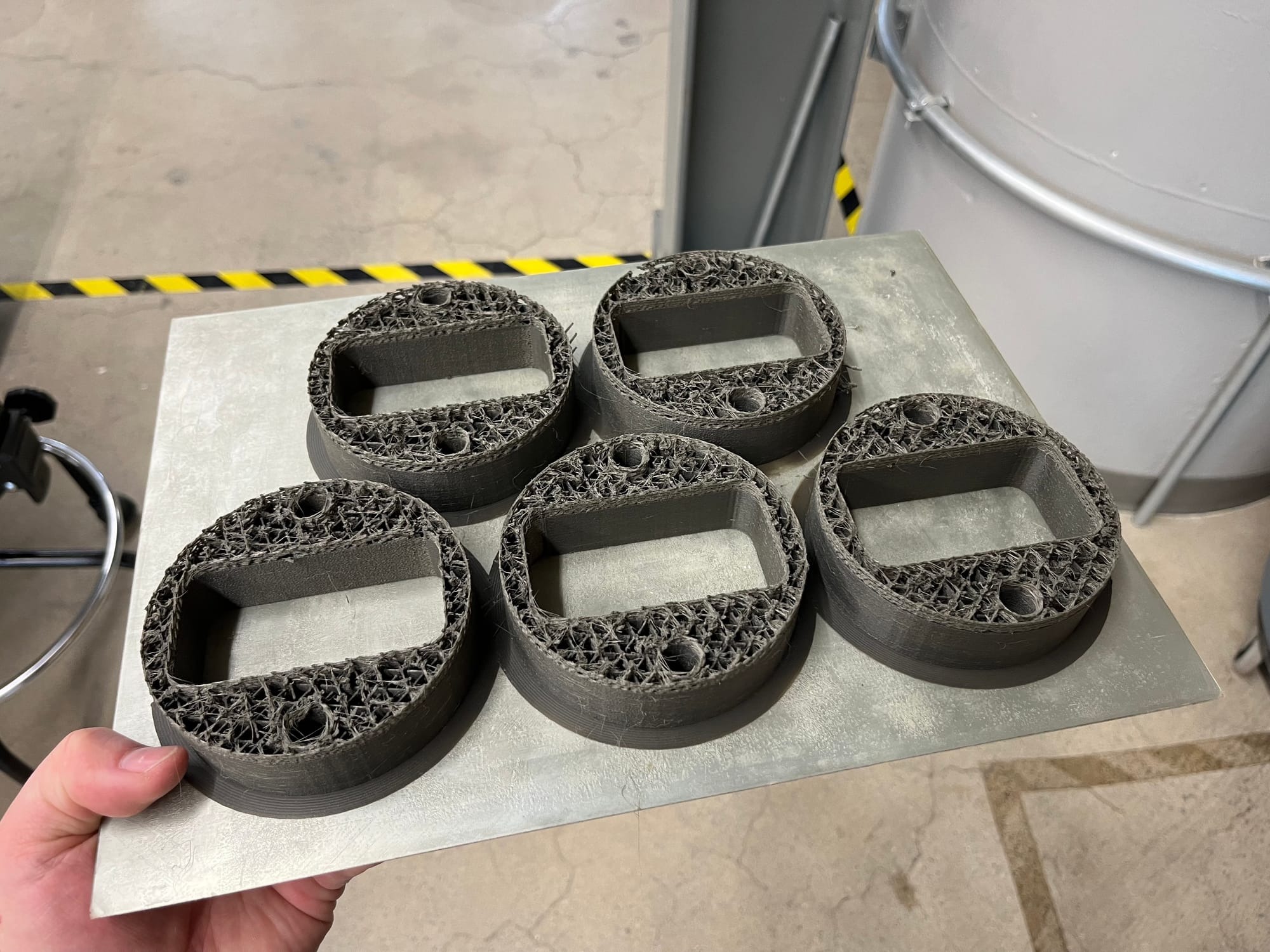
I've started printing parts to fulfill the first order of DB-X buoys. Sometimes it's tough to balance the risk of printing in series or parallel. If you print in parallel, that's to say print 5 parts at the same time for example, the upside is you can leave the machine unattended for 20 or 30 hours. The downside is if you print them at the same time, and the print fails at 75%, you now have 5 unusable parts. Whereas, if you only do a single part at a time, you have to cycle start the machine 5 times, but if a part fails, you've only lost 1 part instead of all 5.
Hydration
No way I drank enough water this week.
Closing Monologue
Spring is in full effect. The weather has been lovely and it feels like it warmed up quicker than in past years. The sun is out! I've been weirdly intentional about planning around sunrise and sunset. Moving errands, chores and meetings around the sun. Why waste an hour of natural daylight grocery shopping in a massive windowless complex pumped full of artificial fluorescent lights, when you could go a little bit later after the sun goes down? Maybe this is an incredibly normal thing people do, that I've just discovered all on my own. Maybe this is completely unhinged and I'm overthinking everything again. Either way...
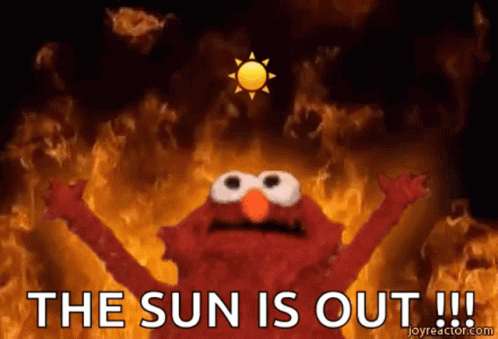
...thanks for reading, and seize the day!